Navigating the world of stainless steel couplings, particularly the 1 2 NPT (National Pipe Taper), can be a daunting task for businesses and professionals alike. However, understanding the nuances and benefits of this specific product is crucial for ensuring efficient and reliable industrial applications. Leveraging decades of industry experience, here’s an exploration of why these couplings are indispensable in the realms of plumbing, gas lines, and other industrial settings.

Stainless steel, renowned for its robust corrosion resistance and longevity, forms the bedrock of many industrial applications. When it comes to couplings, particularly those with a 1 2 NPT specification, stainless steel offers unmatched durability and performance. This specific NPT configuration ensures a secure seal, reducing the risk of leaks in high-pressure systems which is paramount in maintaining operational efficiency and safety.
Experience shows that the choice of material significantly impacts the coupling's performance. Stainless steel, with its ability to withstand extreme temperatures and pressure, stands out as the material of choice. This attribute is particularly critical in industrial environments that are subject to fluctuating conditions, where reliability equates to cost savings and enhanced safety. Industry veterans have noted significant reductions in maintenance costs by switching to stainless steel couplings, due to their high resistance to scaling and corrosion in aggressive environments.
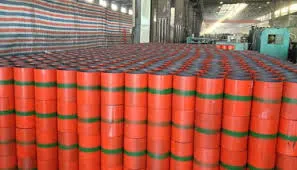
For installations involving fluid transfer, the 1 2 NPT stainless steel coupling's thread design is particularly advantageous. The tapered threads of NPT provide a fluid-tight seal, which is critical in preventing leaks, even under high pressures frequently encountered in industrial pipelines. This precision in design and manufacturing means users can expect a significant reduction in time and resources spent on maintenance.
Authoritative voices in the industry, including engineers and technical specialists, frequently recommend the 1 2 NPT for its versatility and reliability across myriad applications. From the oil and gas sector to chemical processing and water management systems, its application is broad and proven. This endorsement from industry leaders stems from the coupling's ability to ensure systems operate efficiently and safely without unforeseen interruptions.
1 2 npt stainless steel coupling
Trust in product quality is reinforced by rigorous testing and certification processes that these couplings undergo. Accredited by recognized bodies, stainless steel couplings with 1 2 NPT threading adhere to stringent industry standards, providing users with assurances that they are investing in a product that meets global quality specifications. This meticulous attention to quality and detail empowers businesses to plan and operate with confidence, knowing that their infrastructures are supported by components that meet top-tier standards.
Furthermore,
installation and operational flexibility are enhanced when using stainless steel couplings. The installation process is straightforward, reducing labor costs and limiting downtime during installation or replacement. Additionally, their compatibility with other system components, owing to standardized NPT threading, simplifies the integration process in both new and existing setups.
Incorporating the insights from technical experts and field engineers who work directly with these components, the consensus is clear—1 2 NPT stainless steel couplings are an essential investment for any facility aiming to optimize their infrastructure for efficiency, safety, and cost-effectiveness. This coupling product not only delivers on performance but also elevates the overall operational standards of facilities by ensuring seamless and safe fluid transfer.
To conclude, investing in stainless steel couplings with 1 2 NPT specifications is not merely about meeting present needs; it's an investment in future-proofing your operations. Their proven track record of reliability and efficiency positions them as a pivotal element in industrial design and maintenance strategies. Businesses that prioritize high-quality components like these couplings position themselves at the forefront of technological and operational excellence, ensuring their competitive edge in an ever-evolving industrial landscape.