Stainless steel pipe couplings are integral components in a myriad of industrial and domestic piping systems, renowned for their durability and resistance to corrosion. When it comes to joining sections of pipe in various settings—be it in plumbing, chemical processing, or even in the automotive industry—the quality and reliability of the coupling can significantly impact the overall efficiency and safety of the system.

The primary allure of a stainless steel pipe coupling lies in its material properties. Stainless steel, an alloy known for its robustness, combines iron with chromium to create a highly resistant surface to rust and corrosion. This makes stainless steel couplings particularly advantageous in environments exposed to moisture, chemicals, or extreme temperatures. Unlike other metals that may degrade or become brittle over time, stainless steel maintains its integrity, providing a long-lasting solution for integral pipe connections.
In evaluating the design and function of stainless steel pipe couplings, one must consider the specific requirements of the system. There are several types of couplings available, each designed to meet different needs. For instance, threaded couplings allow for easy disassembly, making them perfect for systems that require frequent maintenance. On the other hand, compression couplings provide a secure, leak-proof connection without the need for welding, offering a versatile solution for both temporary and permanent installations.
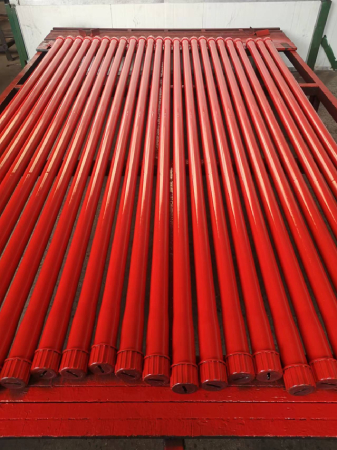
From a technical perspective, the engineering behind these couplings is precise. Manufacturers adhere to strict standards, such as the ASTM A403 specification for wrought austenitic stainless steel, ensuring each coupling delivers performance in demanding scenarios. Expertise in metallurgy is crucial; the exact combination of metal elements can be fine-tuned to cater to specific operational requirements. For instance, increasing the chromium content can enhance corrosion resistance, while adding molybdenum can improve strength and reduce the risk of pitting.
The application of stainless steel pipe couplings extends beyond just joining pipes. These components are engineered to withstand pressures from both the inside (from fluids or gases passing through) and the outside environment. This is especially critical in high-pressure systems where any failure could lead to catastrophic results. In such cases, a hydraulic steel coupling, designed to sustain extreme pressure, becomes invaluable.
1 2 stainless steel pipe coupling
As with any critical component in engineering, trustworthiness is paramount. Ensuring that the coupling fits seamlessly into the broader system requires not only precise machining and design but also rigorous testing. Reputable manufacturers often subject their couplings to tests that simulate the most extreme conditions to guarantee performance. This includes pressure testing, thermal cycling, and even testing for chemical resistance, affirming that the coupling can withstand the environment it will be exposed to.
In addition to their performance capabilities, the aesthetic properties of stainless steel cannot be overlooked. The natural finish of stainless steel couplings is not only functional with its resistance to staining and tarnishing but also visually appealing. This makes them suitable for commercial settings where the visual impact of plumbing fixtures matters as much as their functionality.
Usage of stainless steel pipe couplings in strategic areas, such as joints or bends in pipelines, ensures that costly and time-consuming repairs are minimized. The cost-efficiency of using stainless steel, while initially higher than other materials like PVC or copper, becomes apparent when one considers the reduced need for replacements or repairs over the lifetime of the system.
In sum, the selection of 1 2 stainless steel pipe couplings is not solely a decision based on immediate practicality but a strategic choice that reflects a balance between upfront cost, long-term reliability, and performance endurance. Industry experts and engineers continue to recommend these couplings for complex systems due to their proven track record of reliability and efficiency. As technology progresses and new alloys are developed, the capability and applicability of stainless steel couplings only continue to expand, promising even greater innovation in the future.