For professionals working in sectors such as plumbing, construction, or manufacturing, choosing the right 1 4 inch tube coupling can be a game-changer. Despite being a small component, this essential item plays a critical role in many types of pipe connections and fluid transfer systems. Understanding its nuances is paramount for efficiency, safety, and durability in various applications.

One of the foremost considerations when selecting a 1 4 inch tube coupling is the material. Typically, couplings are made from materials like brass, stainless steel, or plastic. Brass couplings are favored for their durability and resistance to rust, making them ideal for water supply systems. They offer a substantial balance between strength and malleability, ensuring that connections remain tight without being overly rigid. On the other hand, stainless steel couplings are often chosen for their high resistance to corrosion and pressure, making them perfect for industrial environments where chemical exposure is a factor. For applications where weight is a concern and pressure ratings are lower, plastic couplings provide an economical and effective solution.
The second factor to consider is the coupling’s connection type.
Options include push-to-connect, threaded, and compression fittings. Push-to-connect couplings are user-friendly and speed up installation, ideal for non-experts or time-sensitive projects. Such attributes make them popular in residential or DIY applications. Threaded fittings, requiring more expertise, provide a secure and often reusable connection, excellent for systems requiring routine maintenance or adjustments. Compression fittings offer versatile usage, offering tight seals without the need for welding or soldering, and are applicable in both permanent and temporary setups.
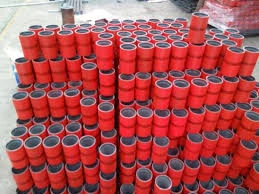
Precision in the manufacturing of 1 4 inch tube couplings also cannot be overstated. Tolerance levels in the production of these components need to be exact. Manufacturers with robust quality control processes ensure that their products consistently meet these precision standards, reducing the likelihood of leaks or system failures. Close examination of technical specifications and industry certifications, such as those adhering to ASTM standards, can offer reassurance regarding a product’s quality and reliability.
A crucial yet often overlooked facet of tube couplings is their influence on system flow rates. Poorly designed or mismatched couplings can lead to pressure drop, which not only decreases efficiency but can also strain pumps and other components in a fluid system, leading to premature wear or failure. It is essential to match the coupling size and type accurately with the system’s flow requirements to maintain optimal performance and extend longevity.
1 4 inch tube coupling
In terms of expertise, consulting with manufacturers or suppliers who provide detailed technical support and documentation can significantly enhance decision-making. Their insights on advanced functionalities, such as temperature or chemical resistance specific to each coupling type, increase productive deployment and system integration.
The impact of these elements reaches its zenith when you consider the cost-to-benefit ratio of selecting the right coupling. Investing in a high-quality 1 4 inch tube coupling may involve a higher initial expenditure, but such an investment often yields long-term financial benefits by minimizing maintenance costs and downtime due to failures. In projects where operational continuity is key, this foresight is invaluable.
Trust in the selected product and its provider is paramount. Leading providers often back their offerings with comprehensive warranties and customer service support. Their commitment to customer satisfaction and transparency regarding product limitations and capabilities establishes a trust foundation, endorsed by testimonials and case studies that demonstrate real-world application successes.
Choosing the right 1 4 inch tube coupling is an important decision with far-reaching implications on project efficiency, safety, and cost-effectiveness. By factoring in materials, connection types, precision, system impact, manufacturer support, and reliability, professionals can make informed choices that will ensure both immediate and lasting results for their projects.