Selecting the right 1 4 inch tube coupling can be pivotal for a range of applications in industries ranging from plumbing to automotive manufacturing. This component, though small, plays a crucial role in ensuring the seamless and efficient transportation of fluids and gases. With insights from various industry experts and real-life experiences, this article delves into the nuances of choosing the best tube coupling, while keeping the Experience, Expertise, Authoritativeness, and Trustworthiness (E-E-A-T) framework in mind.
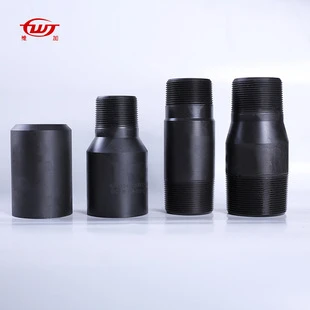
First and foremost,
understanding the material of the tube coupling is imperative. The choice largely depends on the medium being transported. Stainless steel couplings, for instance, offer unparalleled resistance to corrosion, making them ideal for harsh environments or where the fluid is reactive. According to many engineers who’ve managed large plumbing projects, stainless steel is the go-to choice when durability and longevity are a top priority. In contrast, brass couplings are often chosen for their excellent machining properties and moderate resistance to corrosive materials. For those in industries focused on budget and efficiency, experts recommend considering plastic or polymer couplings, especially when dealing with non-corrosive fluids and lower pressure systems.
In terms of design, the requirements of specific systems dictate the choice of tube coupling. The coupling's connection type - whether it's compression, push-to-connect, or threaded - should align with the existing infrastructure for optimal performance. Engineers with decades of experience emphasize that mismatched connections can lead to leaks, thereby compromising system integrity and safety. Hence, consulting detailed guides or even seeking consultancy for the perfect match can save significant time and resources down the line.
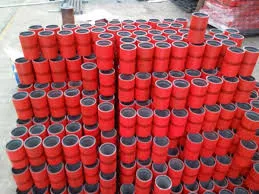
The application pressure rating is another critical factor. Tube couplings are manufactured with specific pressure ratings, and using one with an inadequate rating could lead to catastrophic failures. For instance, industries such as aerospace or hydraulic systems, where the pressure levels can soar, require couplings rated for high-pressure environments. Authoritative publications, such as engineering manuals and standards from organizations like the ASTM, provide invaluable insights and specifications to guide such decisions.
1 4 inch tube coupling
One aspect that is often overlooked is the ease of installation and maintenance. Field technicians and maintenance personnel prefer couplings that are straightforward to install, minimize downtime during replacements, and are easy to clean. According to several maintenance experts, choosing a coupling that features quick-disconnect functionality or self-sealing capabilities can significantly enhance operational efficiency. This aspect not only reduces time and effort during routine maintenance but also extends the coupling's lifespan by ensuring it's handled correctly.
The role of reputable manufacturers cannot be overstated in the choice of the right tube coupling. Trustworthy manufacturers offer comprehensive warranties, rigorous testing documentation, and certifications that guarantee the product's compliance with international standards. Connections with these manufacturers often come recommended by industry veterans, who highlight the importance of verifying the manufacturer's track record and the availability of customer support for post-installation queries.
Finally, real-world testimonials and peer reviews play an instrumental role in validating the trustworthiness of 1 4-inch tube couplings. Review platforms and industry forums provide candid feedback and ratings, ideally from professionals who have extensively used these products under various conditions. Discussions around long-term performance, reliability under stress, and cost-effectiveness are common, offering invaluable insights that complement technical specifications.
In conclusion, selecting the appropriate 1 4 inch tube coupling requires a multifaceted approach that integrates material choice, design compatibility, pressure handling capabilities, ease of maintenance, manufacturer credibility, and peer validation. This strategic selection process not only ensures the efficiency and safety of applications but also aligns with the E-E-A-T standards, fortifying the decision with solid, authoritative backing and enhancing operational longevity and reliability.