The 1 4 pipe coupler is an essential component in many plumbing and industrial systems, offering a seamless connection between pipes that can withstand various pressures and conditions. Having worked extensively in the plumbing supply industry, I can assert that choosing the right pipe coupler is crucial for ensuring system integrity and longevity.
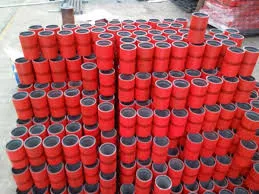
Starting with the components, the 1 4 pipe coupler is typically made from robust materials like brass, stainless steel, or PVC. Each material serves different needs based on the application. Brass couplers are known for their excellent antimicrobial properties and corrosion resistance, making them ideal for water systems. Stainless steel couplers, on the other hand, offer unmatched durability and can handle high-pressure systems, which is why they are often utilized in industrial applications. PVC couplers are lightweight and resistant to chemical reactions, making them ideal for underground or less demanding applications.
In terms of installation, ease and efficiency are paramount.
A crucial aspect of this is ensuring that the coupler provides a leak-proof connection. Proper threading and tight seal-fitting designs ensure that there are no chances of leaks, which could otherwise lead to costly water damage or reduced system efficiency. The 1 4 pipe coupler’s design often includes ridges or threads that allow for an easy and secure fit. It is highly recommended to use Teflon tape or a similar sealing material during installation to enhance the seal and prevent leaks.
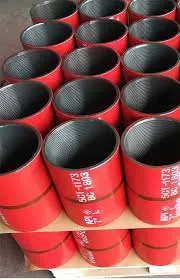
When selecting a 1 4 pipe coupler, considering the environmental conditions is vital. For systems exposed to fluctuating temperatures, opting for a coupler that can withstand thermal expansion is essential. This prevents cracking or deformation, maintaining the integrity of the pipeline. Moreover, in systems where hygiene is critical, such as potable water systems, selecting materials like brass aids in maintaining water quality.
1 4 pipe coupler
In my years of overseeing numerous installations, I have observed that regular maintenance of pipe systems, including periodic inspections of the couplers, can prevent potential failures. Replacing a worn or damaged coupler is a simple process that can save considerable costs and downtime. A visual inspection of the joints and couplers in your system every few months can identify wear or potential failure points early.
For those seeking more advanced solutions, the market has seen innovations such as couplers with built-in pressure and temperature sensors. These smart couplers are an excellent choice for industrial applications, where system monitoring can preemptively avert issues, ensuring that the pipeline functions smoothly without unexpected breakdowns.
The trustworthiness of your pipe coupler supplier also plays a significant role in ensuring product reliability. Partnering with reputable manufacturers who provide certified and tested products can reduce the risk of failure and ensure compliance with industry standards. It is advisable to consult with suppliers who offer warranties on their couplers, reflecting their confidence in the product’s performance and longevity.
For both professionals in plumbing and DIY enthusiasts, understanding the significance of the 1 4 pipe coupler in a system cannot be overstated. Its role as the unsung hero in ensuring seamless connectivity and system efficiency is unparalleled. By selecting the correct coupler material, ensuring proper installation, and maintaining a proactive approach in system upkeep, you can ensure that your pipeline remains efficient and long-lasting. This attention to detail not only supports optimal performance but also fosters a foundation of trust in the quality and reliability of your pipeline infrastructure.