The world of plumbing and mechanical systems often demands components that are robust, reliable, and resistant to the various challenges posed by harsh environments. One such component that has gained significant attention and appreciation is the 1 4 stainless steel coupling. These couplings are not only essential in the proper functioning of systems but also stand as a testament to the advancements in material science and engineering.
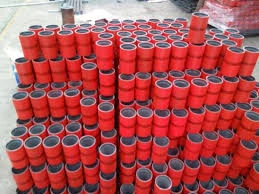
1 4 stainless steel couplings are particularly celebrated for their exceptional durability and resistance to corrosion. Stainless steel, known for its chromium content which gives it a unique resistance to rust, is an ideal material for couplings that are often exposed to moisture, chemicals, and other potentially corrosive elements. This resistance is not just a feature but a necessity in many industries such as oil and gas, water treatment, and construction, where equipment failure could lead to substantial downtime or hazardous situations.
In plumbing applications, the use of a 1 4 stainless steel coupling can significantly enhance the integrity of the system. Its ability to maintain a seal and ensure leak-proof connections even under high pressure and temperature conditions makes it invaluable. Moreover, its compatibility with various types of pipes — whether they be PVC, copper, or galvanized steel — adds to its versatility. This adaptability ensures that the right type of stainless steel coupling can be used in almost any scenario, making it a preferred choice among engineers and contractors.
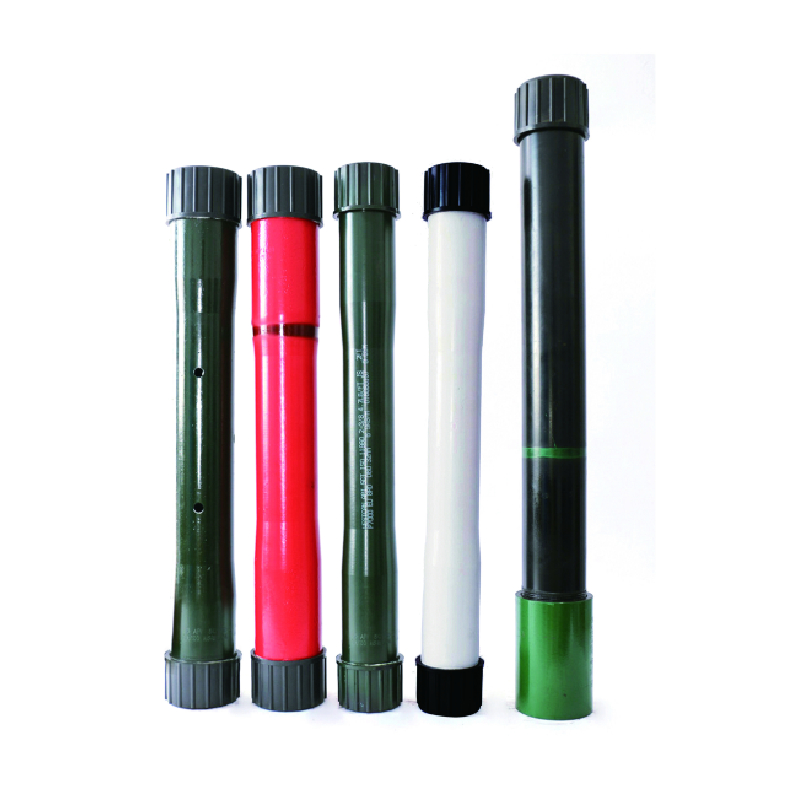
The allure of these couplings also lies in their ease of installation and maintenance. Typically, they require less frequent checks and replacements compared to their counterparts made of lesser materials. This characteristic is particularly attractive for large-scale industrial operations, where maintenance downtime must be minimized to avoid interruption of service and increased costs. Furthermore, their longevity translates into cost savings over time, reducing the frequency of replacements and repairs.
From an expertise standpoint, the manufacturing process of 1 4 stainless steel couplings involves advanced metallurgy and precision engineering. Proper heat treatment and fabrication techniques are essential to ensure that the couplings meet the high standards required in demanding environments. This expertise is not only about producing a component but ensuring that it performs reliably under specified conditions. Manufacturers with extensive experience in the production of stainless steel components are often more trusted, having the necessary quality control measures to back their products.
1 4 stainless steel coupling
The choice of stainless steel grade also plays a critical role in the performance of these couplings. For instance, 316 stainless steel, which contains molybdenum, offers even greater corrosion resistance compared to 304 stainless steel, making it suitable for more severe marine environments and chemical processing applications. In selecting a 1 4 stainless steel coupling, understanding the specific requirements of the application is key to ensuring optimal performance and safety.
For users seeking authoritative advice on 1 4 stainless steel couplings, turning to reputable suppliers or consulting with industry experts can offer significant advantages. These professionals can provide detailed insights into the right type of coupling for specific applications, advice on installation practices, and maintenance tips to prolong the life of the component. Their insights are invaluable, as they draw from a wealth of experience and technical knowledge, ensuring that the right decisions are made.
Trustworthiness in this domain is enhanced by certifications and compliance with industry standards. Look for couplings that meet ISO certifications or other relevant industry standards. This compliance not only assures quality but also safety, which is paramount when dealing with mechanical components that are integral to larger systems.
In conclusion, the 1 4 stainless steel coupling stands out not just because it fulfills a mechanical role but because it embodies a fusion of technological advancement, material expertise, and practical reliability. Its benefits are manifold — from corrosion resistance and durability to ease of maintenance and versatility. Whether in a simple domestic plumbing setup or a complex industrial facility, these couplings represent an investment in quality and reliability, ensuring systems function smoothly and without incident. For those in the industry, their utility and performance are not just appreciated but necessary, making them an indispensable part of modern engineering solutions.