Every industry that relies on fluid transfer systems values the role of a reliable pipe coupler. Among them, the 1 8 pipe coupler stands as a vital component for ensuring seamless connectivity, improved efficiency, and longevity of systems. In this comprehensive guide, we delve into the experiential and expert knowledge surrounding the 1 8 pipe coupler, addressing its significance, functionality, and the principles that make it invaluable in various applications.
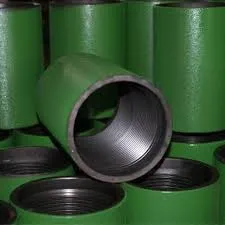
The 1 8 pipe coupler, a specifically engineered component, is designed to join two lengths of pipes together, typically of a smaller diameter, which is crucial in systems that handle fluids or gases. Its sheer versatility allows it to be employed in domestic, industrial, and even high-tech environments. The term 1 8 often refers to sizes or specific standards which render the coupler suitable for specific applications, indicating a level of precision and custom-fit unmatched by generic variants.
Over the years, the design and construction of pipe couplers have seen significant advancements. Built with enduring materials such as stainless steel, brass, and eco-friendly polymers, 1 8 pipe couplers offer impressive corrosion resistance and mechanical durability. Experts insist that selecting the right material is critical based on the application to enhance the performance and lifespan of the pipeline systems they are integrated within. For example, in corrosive environments, using brass or high-grade stainless steel could vastly improve reliability.
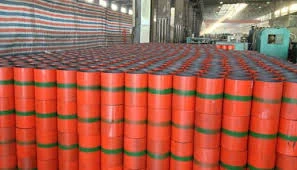
A notable aspect of the 1 8 pipe coupler is its seamless integration with modern-day piping infrastructure. Engineers commend its design that minimizes fluid friction, thereby enhancing the flow efficiency. This is particularly evident in systems where maintaining a specific fluid pressure is crucial. By ensuring minimal leakage and optimal seal integrity, these couplers stand as a testament to engineering excellence.
1 8 pipe coupler
In terms of authoritativeness, the 1 8 pipe coupler often adheres to strict industry and international standards, including ISO certifications and ANSI/ASME specifications. These standards guarantee that each product is manufactured to meet rigorous quality control measures, providing consumers with a trusted solution that aligns with global safety and performance benchmarks. Installers and operators are thereby assured of the coupler's reliability, reducing downtime and maintenance costs.
Field experience further solidifies the trustworthiness of these components. Frequently adopted by leading engineering firms and home builders, real-world applications showcase their pivotal role in sustaining the integrity of piping systems. For instance, in chemical plants and refineries, the precise role of a 1 8 pipe coupler can prevent catastrophic failures, ensuring safe transport of potentially hazardous materials.
When selecting a 1 8 pipe coupler, several factors must be taken into account beyond just material and size. Pressure ratings, temperature resistance, and compatibility with existing components are critical considerations. An expert recommendation is to always pair the coupler with the appropriate fittings and tools to ensure a perfect match and secure installation.
In conclusion, the 1 8 pipe coupler exemplifies a blend of innovation, safety, and functionality. Its comprehensive applications across varied sectors reaffirm its necessity in modern fluid dynamics and pipeline engineering. By embracing such specialized components, industries not only adhere to high-quality engineering practices but also fortify the dependability of their systems, underscoring the coupler's indispensable role in today's technological landscape. Adopting this centered approach only elevates the system's performance, providing stakeholders with tangible benefits and underscoring the perpetual evolution of piping solutions.