Stainless steel couplings serve as vital components in various piping and mechanical systems, owing to their durability, corrosion resistance, and superior strength. Users across industries from plumbing to automotive manufacturing rely on these couplings to ensure seamless integration and efficient operation of their systems. A strong grasp of the features and advantages of stainless steel couplings is crucial for professionals seeking to maximize the performance and reliability of their projects.

Stainless steel, renowned for its anti-corrosive properties, forms the backbone of these robust couplings, ensuring longevity and reliability even under extreme conditions. Industries that require components to withstand various environmental and chemical exposures, such as marine, oil and gas, and chemical processing, find stainless steel couplings indispensable. The material's inherent resistance to rust and staining not only extends the lifecycle of the coupling but also maintains the integrity and safety of the entire system.
From an expertise standpoint, it is essential to understand the different types of stainless steel available for coupling applications. The most common grades include 304 and 316 stainless steel. Grade 304 offers excellent corrosion resistance and is suitable for most applications, while 316 stainless steel provides even higher resistance to chloride and acidic environments, making it ideal for more demanding environments.
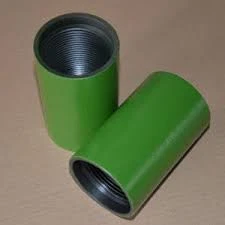
Moreover, the design and engineering behind these couplings focus on ensuring leak-free connections. Precision-engineered threads and gaskets are key features that prevent leakage, a critical factor in industries requiring high precision and safety standards. When selecting a coupling, attention to detail in the manufacturing process, such as compliance with international standards and certifications, reflects the manufacturer's commitment to quality and reliability.
1 stainless steel coupling
In terms of authoritativeness, leading manufacturers often provide detailed documentation and support as part of their commitment to customer satisfaction. This includes installation guides, maintenance tips, and compatibility charts, ensuring users can effectively integrate the coupling into their systems without undue complications. Companies with rigorous quality control measures and third-party certifications often stand out as authoritative suppliers in this field, upholding the highest industry standards.
Trustworthiness is further built through customer experiences and feedback. As real-world applications of stainless steel couplings are diverse, user testimonials and case studies provide invaluable insights into the product's performance across different scenarios. These authentic experiences highlight not only the benefits of using stainless steel couplings but also potential challenges and solutions from practical usage, adding layers of trust for prospective buyers.
One significant advantage of stainless steel couplings is their versatility. They can be utilized across a vast array of connection systems including threaded, welded, or even mechanically attached variants. This adaptability ensures that regardless of the system specifications or design constraints, there is a stainless steel coupling solution available. This versatility translates into operational efficiency and cost-effectiveness, allowing engineers to streamline their equipment and reduce downtime.
In conclusion, stainless steel couplings epitomize the intersection of durability, reliability, and versatility, making them indispensable in modern industry piping and mechanical system designs. Their superior resistance to weathering and chemical exposure secures system integrity and extends the lifespan of the complete installation. By understanding the nuances of material choice, engineering excellence, manufacturer reputation, and real-world application feedback, professionals can confidently select the optimal coupling for their specific needs, ensuring both performance and peace of mind.