Steel couplings serve as essential components in numerous mechanical and industrial applications, providing the essential function of connecting two shafts together. Not only do they facilitate the efficient transmission of power and torque, but they also compensate for slight misalignments that might otherwise cause significant wear or damage. A deep dive into the world of steel couplings reveals their indispensable role across various sectors, where reliability, durability, and precision are key.
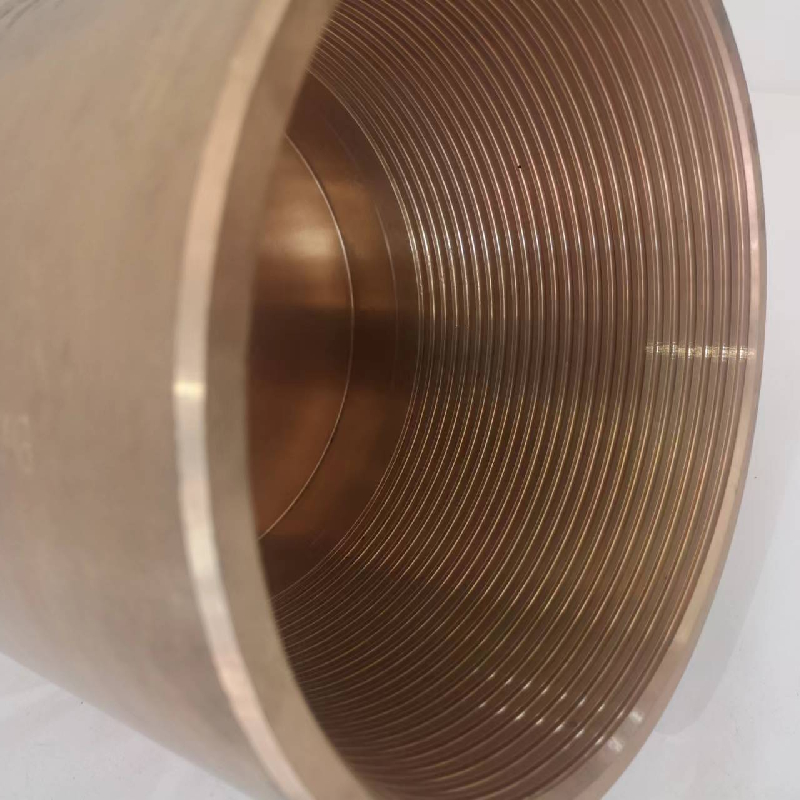
Experience shows that selecting the right type of coupling directly impacts the performance and longevity of the entire system it serves. Notably, the choice of material—steel, in this context—confers several advantages. Steel is known for its strength and durability, capable of withstanding high torque and harsh environments without succumbing to wear and tear. This is particularly evident in sectors such as manufacturing and construction, where machinery is routinely exposed to demanding conditions.
An expert understanding of the various types of steel couplings can aid in making informed decisions tailored to specific needs. Flexible steel couplings, for example, are designed to accommodate misalignments while transmitting torque smoothly. This flexibility proves crucial in applications where alignment precision is challenging to maintain, such as in dynamic environments where equipment is subject to shifting forces. Rigid steel couplings, on the other hand, are ideal for applications demanding precise shaft alignment with no room for movement, ensuring perfect synchronization between two connected shafts.
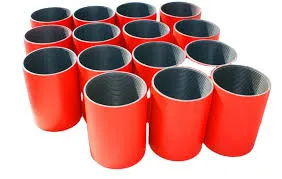
The authority of steel couplings in the industry stems from their proven record of reliability. In sectors such as automotive manufacturing and heavy machinery, the need for components that guarantee uninterrupted operation over long periods is paramount. Steel couplings meet and often exceed these expectations, which is why they are consistently favored by industry-leading manufacturers globally. The high tensile strength of steel ensures that these couplings can endure substantial loads, a critical factor in applications involving large machinery or prolonged operations.
Trustworthiness is built not just on performance but also on adherence to international standards and regulations. Reputable manufacturers of steel couplings adhere to stringent quality control processes, ensuring that every product meets the necessary specifications for safety and efficiency. This commitment to quality is vital, as any failure due to substandard components could lead to costly downtime or even catastrophic failures, especially in critical industrial operations.
1 steel coupling
For professionals looking to invest in steel couplings, understanding these elements is vital. It not only aids in the selection process but also ensures that the couplings chosen will deliver as expected, supporting operation integrity and efficiency. Furthermore, regular inspections and maintenance are recommended to uphold the reliability of these components. While steel couplings are resistant to wear, proactive maintenance ensures that any potential issues are identified and addressed before they escalate.
Navigating the complexities of coupling selection is made easier with access to comprehensive resources and expertise. Many manufacturers provide detailed guides and support, allowing their clients to make choices backed by data and empirical evidence. Such resources enhance the decision-making process, providing a balance between theoretical knowledge and practical application.
Steel couplings, therefore, represent a cornerstone of modern mechanical and industrial engineering practices. Their versatility and robustness underline their critical role in keeping machinery running smoothly and efficiently. As industries continue to evolve, the demand for high-quality steel couplings is expected to grow, mirroring the broader trend towards optimization and reliability in industrial operations.
In conclusion, the steel coupling is more than just a mechanical component; it embodies the principles of durability, precision, and reliability. For any entity involved in machinery maintenance or industrial operations, understanding and utilizing these components ensures improved performance and operational longevity, which are indispensable for maintaining competitive advantage in today’s fast-paced industrial landscape.