The world of industrial fittings and pipeworks presents various materials to consider, with stainless steel being a standout choice due to its durability and resistance to the elements. Specifically, when discussing couplings, the 3 8 stainless steel coupling emerges as a pivotal piece in both specialized and general plumbing applications. Renowned for its robust properties, versatility, and longevity, this stainless steel coupling meets, if not exceeds, the demands of both novice DIY enthusiasts and professional plumbers.

Understanding the material composition of 3 8 stainless steel couplings is crucial in appreciating their value.
Stainless steel is an alloy known for its corrosion resistance, primarily due to the presence of chromium. Typically, the composition of 3 8 stainless steel includes approximately 18% chromium, making it particularly adept at resisting rust and corrosion even in aggressive environments such as saltwater exposure or chemical processing plants. This inherent resistance means the coupling can withstand extreme temperatures and maintain its structural integrity, a necessity in industries focusing on sanitary processing or those utilizing high-pressure systems.
The versatility of the 3 8 stainless steel coupling cannot be overstated. Its application spans various industries, whether in food and beverage, pharmaceuticals, automotive, or construction. The coupling's design accommodates the seamless connection between pipes of various sizes and types, ensuring that systems maintain optimal flow rates without the risk of leakage. This adaptability is essential in industries where downtime due to maintenance or repairs can lead to significant production losses.
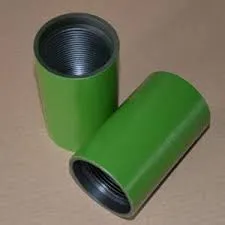
Moreover, the coupling's design supports easy installation, which enhances its appeal, particularly in scenarios requiring quick setups or last-minute adjustments. The precision engineering seen in stainless steel couplings reflects years of metallurgical advances and exhaustive testing, aimed at fulfilling industry standards and surpassing user expectations. Such efficiency illustrates expertise in material science and engineering, establishing 3 8 stainless steel couplings as a trusted component in complex systems.
3 8 stainless steel coupling
Authoritative voices in the plumbing and industrial maintenance sectors frequently highlight the reliability and trustworthiness of stainless steel components. An extensive body of research and field reports confirms that installations utilizing these couplings exhibit longer lifespans, reduced maintenance costs, and improved safety records. These endorsements are not merely anecdotal; they are supported by rigorous testing under various operational pressures and environmental conditions, reinforcing the coupling's standing as a dependable industry staple.
The trustworthiness of 3 8 stainless steel couplings is further bolstered by consistent quality control checks that manufacturers implement to adhere to internationally recognized standards such as ASTM and ISO. These checks ensure that each piece produced meets stringent specifications for both material and performance, thereby minimizing the risk of failure and enhancing user confidence.
For the end-user, there is an inherent assurance when opting for stainless steel couplings, particularly of the 3 8 size, which aligns well with both large-scale infrastructural projects and smaller domestic tasks. The coupling’s size and material properties provide an ideal combination of flexibility and strength, often exceeding the performance of alternative materials such as cast iron or basic steel variants.
In conclusion, the 3 8 stainless steel coupling is a critical element within the industrial and residential piping landscape, backed by a solid reputation for quality and performance. The coupling’s material composition, ease of application, and adherence to high industry standards demonstrate an unparalleled level of expertise. Consequently, this ensures its established position as a reliable and effective solution, capable of withstanding the demands of diverse operational environments. As industries continue to evolve, the role of such components remains essential, driven by an ever-present need for materials that promise not only technical excellence but also robust reliability.