Stainless steel is a material renowned for its durability, corrosion resistance, and aesthetic appeal.
One of its applications that exemplifies these qualities in industrial settings is the 3-8 stainless steel coupling. This product demands attention not just for its practical uses but for its implicit assurance of reliability and longevity in varying environments.
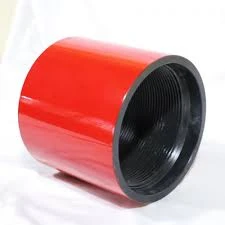
Understanding the Impact of Material Composition
What sets 3-8 stainless steel couplings apart is primarily its material composition. Stainless steel, known for its chromium, nickel, and molybdenum content, offers superior resistance to rust and chemical damage, a crucial factor when assessing product lifespan in industries like plumbing, automotive, and marine applications. The 3-8 coupling, being a part of this robust material family, inherits these traits, making it an ideal choice when reliability cannot be compromised.
Applications and Versatility
The 3-8 stainless steel coupling is pivotal in connecting two distinct shafts together, transferring torque, and accommodating slight misalignments, which might be unavoidable in complex machinery. This coupling finds its place in various industries, from the robust movements seen in heavy machinery and conveyance systems to the precise operations within oil & gas or chemical processing. Its versatility is underscored by the range of temperatures it can withstand without compromising performance, particularly in thermally rigorous environments like those found in power generation plants.

The Structural Efficiency and Technical Specifications
Couplings need to maintain structural integrity under pressure differentials and other operational stresses. The 3-8 stainless steel coupling achieves this with its precision-engineered design, ensuring optimal fit and minimal backlash. The dimensional accuracy is crucial, ensuring that the rotational motion is smooth and synchronized. These technical specifications are vital for industries that operate under high safety and performance standards, given the disastrous consequences of coupling failures.
Proven Efficiency through Real-World Application
Across numerous industries, decision-makers have recounted the significant improvements noticed upon the integration of 3-8 stainless steel couplings. For instance, a mid-size manufacturing plant specializing in conveyor belt systems documented a 30% reduction in maintenance downtime post-implementation. This is attributed to the durability and less frequent need for adjustments, which, over time, translated to substantial cost savings and increased production efficiency.
3 8 stainless steel coupling
Expert Recommendations and Industry Best Practices
Experts emphasize the importance of selecting the right type of stainless steel coupling based on industry-specific demands. For high-corrosive environments, ensuring the coupling adheres to industry standards, such as ASTM and ANSI, is vital. Proper installation is equally crucial; even a highly durable coupling can fall short if not installed correctly. Experts suggest periodic inspection schedules to preemptively address wear and tear, although the long-lasting nature of stainless steel significantly extends these intervals.
Quality Assurance and Reliable Manufacturing
For businesses considering the transition to stainless steel couplings, trust in manufacturing quality is paramount. Sourcing from certified manufacturers who reinforce stringent quality control offers reassurances of product reliability. Moreover, manufacturers that can authenticate their claims with standards compliance and material traceability reports allow businesses to instill confidence in their operational infrastructure.
Trust and Authority in Supplier Relationships
When purchasing 3-8 stainless steel couplings, fostering a relationship with the supplier is integral. Suppliers who are open about their product pipelines, offer post-purchase support, and provide detailed product documentation enable end-users to make informed decisions. Transparent transactions with potential for customization mark the difference between generic equipment suppliers and specialized partnership providers.
Conclusion
Selecting and implementing the 3-8 stainless steel coupling represents more than a transactional decision. It's an investment in operational durability, increased efficiency, and financial prudence. As industries evolve, advancing towards components that assure performance sustainability becomes critical, ensuring that enterprises are not only maintaining current standards but are poised for future demands. Thus, incorporating stainless steel couplings embodies a forward-thinking approach to technological adaptation and industrial resilience.