In the evolving landscape of technology and engineering, the concept of 5 16 union coupling emerges as a crucial element for companies seeking seamless connectivity and integration in their systems. As industries push towards smarter and more efficient solutions, understanding the nuances of this coupling technique becomes imperative.
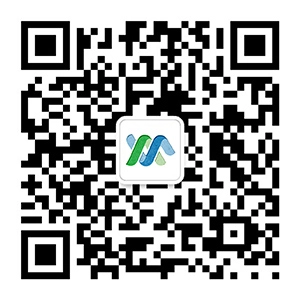
A union coupling, in general, serves the purpose of connecting two pipes or tubes, allowing for easy assembly and disassembly without causing deformation. The term 5 16 union coupling specifically pertains to couplings designed for 5/16 inch diameter pipes or tubes. This specification is frequently employed in industries requiring precise and durable connections under varying pressures.
One of the standout features of 5 16 union couplings is their versatility. They are commonly used in applications ranging from automotive systems to industrial machinery, making them a staple in an engineer's toolkit. Their design often includes robust materials like stainless steel or brass, which provide exceptional resilience against corrosion and wear. This robustness not only ensures longevity but also enhances the safety of the systems they are used in, thus meeting the industry's stringent reliability standards.

From an expert's viewpoint, selecting the right 5 16 union coupling involves a careful analysis of the operational environment. Factors such as temperature fluctuations, pressure requirements, and the chemical properties of the transported fluid must be considered. A coupling's compatibility with these factors can significantly influence the efficiency and safety of the entire system.
Experience from the field highlights that improper selection or installation of union couplings can lead to issues such as leaks or system failure. Therefore,
consulting with professionals who have hands-on experience becomes invaluable. They can provide insights on installation techniques, ensuring that the couplings are fitted correctly and securely, which reduces the risk of future operational problems.
5 16 union coupling
Authoritative sources recommend regular maintenance checks to ensure longevity and optimal performance of 5 16 union couplings. This involves routine inspections for signs of wear or damage and verifying that the fittings remain tightly secured over time. Implementing a preventive maintenance schedule can mitigate risks associated with unexpected downtimes, thereby enhancing system reliability and efficiency.
In terms of trustworthiness, opting for products from reputable manufacturers is crucial. These companies adhere to rigorous manufacturing standards and quality controls, ensuring that their 5 16 union couplings meet the required industry certifications and standards. Additionally, manufacturers with a proven track record provide comprehensive support and documentation, such as installation guides and technical data sheets, which are essential resources for engineers and technicians.
The future of 5 16 union couplings looks promising as advancements in technology introduce new materials and improved design techniques. Innovations in digital simulation and testing are enabling manufacturers to create coupling systems that not only meet current demands but also anticipate future requirements. These enhancements include better resistance to environmental stresses and adaptability to novel applications, underscoring the ongoing evolution of union couplings.
In conclusion, mastering the application of 5 16 union couplings is a testament to a company's commitment to quality, safety, and efficiency. By leveraging expert knowledge, prioritizing experience-based insights, ensuring adherence to authoritative guidelines, and fostering trust through reliable products, industries can harness the full potential of these small but mighty components. Whether in traditional settings or cutting-edge applications, 5 16 union couplings will continue to play a pivotal role in connecting systems with precision and reliability.