Aluminum pipe couplings and fittings are indispensable components in many industries, valued for their durability, versatility, and lightweight nature. These attributes make them ideal for a plethora of applications, from plumbing systems to complex industrial tasks. For professionals seeking reliable materials, understanding the nuances of aluminum components is crucial for optimizing their use in various projects.

One of the major advantages of aluminum pipe couplings and fittings is their exceptional resistance to corrosion. This characteristic is particularly beneficial in environments subject to moisture, such as marine or outdoor applications, where other materials might deteriorate over time. Unlike iron or steel, aluminum forms a protective oxide layer that shields it from further corrosion, thus ensuring longevity and maintaining structural integrity.
Moreover, aluminum's lightweight nature is a significant factor in industries where reducing weight is a priority. In the aerospace and automotive sectors, for instance, using aluminum fittings can contribute to overall weight reduction, enhancing fuel efficiency and performance. Similarly, in construction, these fittings ease the transportation and installation process, reducing labor and time costs without compromising strength or reliability.
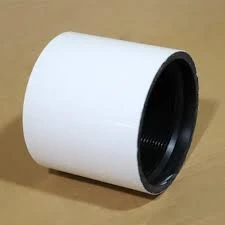
The versatility of aluminum for coupling and fitting applications cannot be overstated. Its malleability allows it to be molded into various shapes and sizes, accommodating a wide range of design specifications without sacrificing mechanical properties. Whether for large-scale infrastructure or delicate instrumentation, aluminum fittings can be precisely tailored to meet specific requirements, showcasing the material's adaptability.
Professionals in the field often highlight aluminum's thermal conductivity as another point of interest. This property is especially advantageous in applications involving heat exchanges, where materials need to efficiently transfer heat without degrading in performance. Aluminum's ability to withstand high temperatures while dissipating heat makes it a preferred choice in HVAC systems, power plants, and other thermal applications.
aluminum pipe couplings and fittings
While experience with aluminum pipe couplings and fittings underscores their many benefits, it's also vital to consider the expertise required for proper installation and maintenance. Despite their resilience, aluminum components must be installed correctly to prevent potential issues such as galvanic corrosion when in contact with dissimilar metals. Experienced technicians ensure that these fittings are integrated within systems in a way that maximizes their longevity and effectiveness.
The authority of aluminum as a material choice is further reinforced by its widespread adoption across various global industries. Standards and certifications set by organizations such as ASTM International and the Aluminum Association provide benchmarks for quality and performance, ensuring that products meet rigorous criteria. Those seeking to procure aluminum couplings and fittings should look for compliance with these standards as a testament to their quality and reliability.
Trust in aluminum pipe couplings and fittings is also bolstered by ongoing advancements in manufacturing technologies. Innovations such as extrusion and advanced alloying techniques have expanded aluminum's capabilities, enhancing its strength and reducing costs. As industries continue to evolve, these innovations ensure that aluminum remains at the forefront of material choices for coupling and fitting applications.
In conclusion, aluminum pipe couplings and fittings offer a combination of durability, versatility, and efficiency that few other materials can match. Their resilience to environmental conditions, lightweight nature, and thermal conductivity position them as a go-to solution for professionals across diverse fields. With proper handling and adherence to industry standards, aluminum fittings continue to set benchmarks for performance and reliability, reinforcing their status as a trusted component for modern engineering challenges.