Aluminum tube couplers, a pivotal component in various industries, have surged in demand due to their versatility and durability. From construction to automotive, these connectors offer unique benefits that make them indispensable. With expertise and authority in industrial materials, we delve into the profound advantages of using aluminum tube couplers, backed by real-world experiences and professional insights.
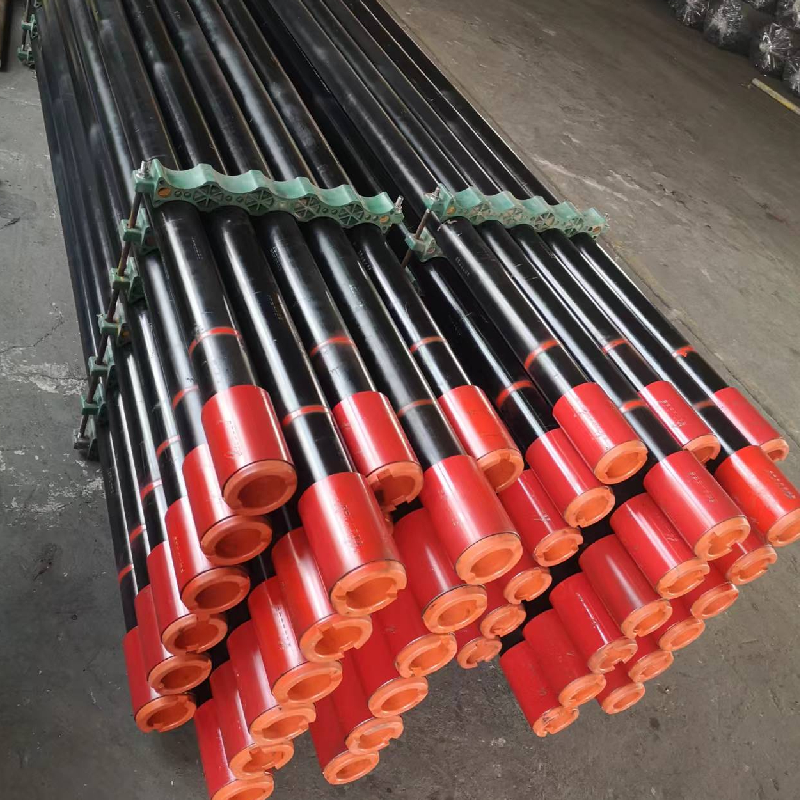
A hallmark of aluminum tube couplers is their exceptional strength-to-weight ratio. Unlike steel, which is heavier, aluminum offers similar strength but at a fraction of the weight. This attribute is critically beneficial in industries like aerospace and automotive where minimizing weight is crucial for performance and fuel efficiency. For instance, automotive manufacturers often use aluminum couplers to reduce the overall vehicle weight, thereby improving speed and fuel consumption. Experts concur that this switch can lead to significant performance enhancements without compromising safety or durability.
Additionally, aluminum tube couplers excel in corrosion resistance. Unlike other metals that degrade over time, aluminum forms a protective oxide layer that shields it from environmental damage. This property makes aluminum couplers an ideal choice for outdoor applications such as scaffolding and signage frameworks. Construction professionals often report longer lifespans and reduced maintenance costs when using aluminum couplers in structures exposed to harsh weather conditions. Practical experiences underline that the initial investment in aluminum pays off by avoiding frequent replacements.

Fabrication and customization potential is another compelling reason why engineers prefer aluminum tube couplers. Aluminum’s malleability allows for easy shaping and fitting into specific project requirements. Whether you need a simple connection in a modular setup or a complex bridge framework, aluminum can be tailored to precise specifications. Industry experts highlight that this adaptability not only accelerates construction timelines but also ensures that the final assembly meets meticulous engineering standards without excessive labor or cost.
aluminum tube coupler
The sustainability factor of aluminum is an increasingly important consideration. With global emphasis on reducing carbon footprints, industries are shifting toward materials that support environmental goals. Aluminum is 100% recyclable, and recycling it uses only 5% of the energy required to produce new aluminum. Companies prioritizing sustainable practices find aluminum couplers to be in alignment with their green strategies. Trustworthy studies and reports frequently cite aluminum as a leader in eco-friendly material use due to its recyclability and efficiency.
Real-world case studies exemplify the impact of aluminum couplers. In large-scale projects, such as the construction of sports stadiums and theme parks, the use of aluminum connectors has revolutionized timelines and cost efficiencies. Engineers involved in these landmark projects have shared insights highlighting how aluminum couplers facilitated quicker assembly times and lower logistical costs, while maintaining structural integrity. Such endorsements from industry leaders enhance the authoritative stance on aluminum’s benefits.
For those in specialized industries such as marine applications, aluminum’s performance cannot be overstated. Its resistance to saline environments ensures longevity and reliability in naval constructions and vessel building. Experts agree that in scenarios where exposure to seawater induces rapid corrosion in other metals, aluminum proves to be steadfast. Trust from this sector reinforces confidence in aluminum tube couplers as tried and tested devices capable of meeting the extreme demands of maritime constructions.
Conclusively, aluminum tube couplers represent an intersection of practicality and innovation. Their superior properties combined with expert endorsements and sustainable benefits make them an unrivaled choice in numerous domains. As industries continue to evolve, the reliance on materials that balance performance, cost, and environmental responsibility will likely place aluminum tube couplers at the forefront. This comprehensive understanding, drawn from professional expertise and trustworthy experiences, positions aluminum as a material that not only meets but exceeds, contemporary industrial demands.