Choosing the right API casing sizes for your industrial applications can be a challenge, yet it’s a critical element that influences operational efficiency and safety. API casing is a vital component in the drilling and completion of oil and gas wells. It is designed to withstand the pressure and stress exerted by both natural formations and the equipment used during the drilling and extraction processes. This article delves into the intricacies of API casing sizes and offers insights based on professional expertise and industry authority, ensuring you make informed decisions based on reliability and trustworthiness.
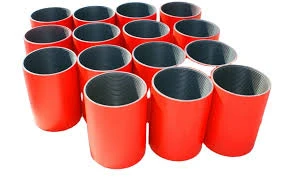
Understanding API Casing Sizes
API casing sizes refer to the different diameters and thicknesses of pipes used in well construction. The American Petroleum Institute (API) sets these standards to ensure uniformity and reliability in the materials used across the industry. The casing serves multiple purposes it prevents the collapse of the borehole, isolates different zones of pressure, and provides a secure conduit for the flow of hydrocarbons. Selecting the appropriate size is crucial for structural integrity and operational success.
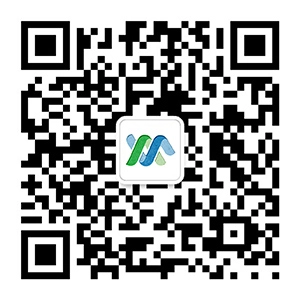
Key Considerations for Selecting API Casing Sizes
1. Well Design and Depth
The design of the well, including its anticipated depth, dictates the required casing sizes. Deeper wells generally require thicker casings to withstand higher pressures. The well's diameter also influences casing size choices, aligning with the diameter of the drill bit.
2. Formation Pressure
The pressures exerted by the geological formations must be considered when selecting casing sizes. Higher formation pressures necessitate thicker casing walls to prevent failure and ensure safety.
3. Environmental Conditions
The external environment, whether offshore or onshore, extreme temperatures, and corrosive conditions play a significant role. Specialized casing materials and designs, such as corrosion-resistant alloys, may be necessary.
4. Regulatory Compliance
Compliance with regional and international regulations is essential. API casing sizes conform to strict standards that ensure safety and environmental protection.
api casing sizes
5. Cost-Efficiency
While larger and thicker casings increase initial costs, they often result in long-term savings by reducing the risk of accidents and equipment failure. It's essential to balance the upfront investment against potential future gains.
Industry Expertise and Insights
As an industry veteran, the importance of collaborating with experienced manufacturers cannot be overstated. Seek out manufacturers known for their adherence to API standards and reputation for quality and innovation. Their expertise in metallurgy and engineering contributes significantly to the development of high-performing casing solutions.
Moreover, ongoing training and updates in technological advancements are vital. Engaging with industry experts and participating in forums and conferences can provide invaluable insights into the latest trends and improvements in casing technology.
The Role of Technology in Casing Selection
Emerging technologies, such as computer simulations and stress analysis software, play a crucial role in determining optimal casing sizes. These tools allow engineers to model various scenarios and stressors, thereby optimizing design before actual implementation. Leveraging such advanced technologies ensures precision and enhances the reliability of the selected casing sizes.
Conclusion
The correct selection of API casing sizes is fundamental in ensuring the operational success and risk mitigation of drilling activities. By aligning well design with appropriate casing, accounting for environmental and pressure conditions, and employing industry expertise, companies can safeguard their operations and enhance their overall performance. Always prioritize quality and compliance, and stay abreast of evolving technologies to maintain a competitive edge in the demanding field of oil and gas extraction.