In the intricate world of oil and gas extraction, API tubing couplings play a pivotal role in ensuring the seamless operation of downhole tubing systems. These small, yet mighty components, connect segments of tubing, allowing for the safe and efficient transport of oil and gas from deep beneath the earth’s surface to the production facilities. To grasp the true significance of API tubing couplings, one must delve into their technical finesse, utilitarian value, and the stringent standards that govern their manufacturing.
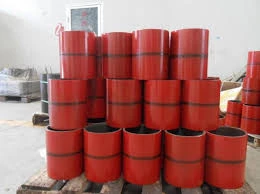
Experience within the industry highlights that API tubing couplings must withstand extreme conditions, including high pressures, corrosive environments, and immense tensile stresses. Over the years, operators have reported how inferior couplings can lead to catastrophic failures, such as leaks or blowouts, emphasizing the necessity for high-quality components to mitigate operational risks. Hands-on field experience consistently points to the use of premium couplings as a best practice, significantly enhancing overall well performance and reliability.
Experts in the field of petroleum engineering and metallurgy underscore the importance of material selection and precision machining in the production of API tubing couplings. Leading manufacturers utilize high-strength steel grades, such as J55, N80, L80, and P110, which are selected based on their ability to endure the specific temperature, pressure, and chemical conditions of each well. State-of-the-art machining ensures that threads match perfectly, reducing the likelihood of failures that can disrupt operations.

Authoritativeness in the production of API tubing couplings is underscored by adherence to the specifications set forth by the American Petroleum Institute (API). These standards, such as API 5CT, outline the requirements for design, material, manufacture, and testing of the couplings. Compliance with API standards ensures that couplings meet the rigorous demands of modern drilling and production. Companies that achieve API certification demonstrate a commitment to quality and safety, establishing themselves as trusted leaders in the industry.
api tubing couplings
Trustworthiness remains a cornerstone for suppliers of API tubing couplings. Users in the industry frequently seek out manufacturers who not only comply with API standards but also engage in continuous testing and quality assurance. Real-world testimonials from rig operators and field engineers often highlight the importance of choosing suppliers with proven track records. Transparent communication about product performance, backed by rigorous third-party testing, fosters trust and loyalty among customers.
Furthermore, the evolution of technology in the oil and gas industry is driving innovation in the design and functionality of API tubing couplings. Solutions such as anti-corrosion coatings and advanced thread designs are setting new benchmarks for performance. These technological advancements are not merely add-ons but essential upgrades that extend the life and efficiency of downhole tubing systems.
In conclusion, API tubing couplings are critical components that have a far-reaching impact on the efficacy and safety of oil and gas operations. Leveraging both experience and expertise, operators can make informed decisions that enhance system reliability and performance. By choosing products that are engineered and authenticated to the highest industry standards, companies establish a foundation of trust and authoritative competence that defines success in the demanding landscape of energy production. As the industry continues to evolve, the demand for high-quality, innovative coupling solutions that meet and exceed API standards will remain ever-present, shaping the future of oil and gas exploration and production.