In the realm of oil and gas extraction and transmission, ensuring the efficiency and safety of operations hinges significantly on the quality of the equipment used.
One essential component in the configuration of oil extraction machinery is the API tubing coupling. These couplings serve a critical function in connecting segments of tubing, forming a continuous string that can efficiently convey oil and gas to the surface.
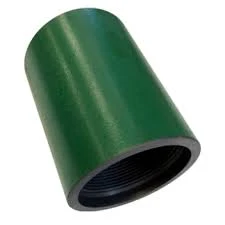
Recent innovations have underscored the importance of coupling quality, especially in high-stakes drilling environments. A robust API tubing coupling is crucial, given the coupling interfaces between the dynamic environments of downhole operations and surface systems. The integrity of these connections can affect well productivity, safety, and operational efficiency, hence the meticulous adherence to standardized criteria.
There are several reasons why API (American Petroleum Institute) standards dominate the conversation in tubing couplings. Firstly, these standards ensure compatibility across global operations, granting ease in equipment replacements and collaborations between international operators. The universal application of API 5CT specifications, which define tubing sizes, materials, and performance characteristics, ensures that operations meet consistency in safety and performance criteria. Operators who prioritize API-standard couplings are frequently positioned to remain adaptable, reducing downtime due to equipment failures and mismatches.
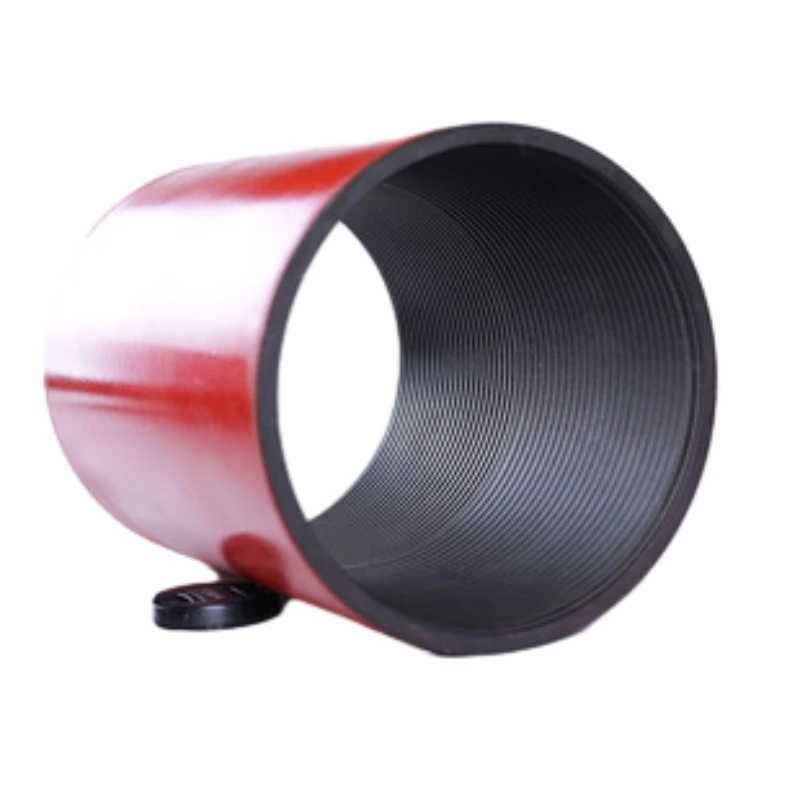
In discussing the expertise required to produce high-quality API tubing couplings, it’s essential to recognize the precision in manufacturing and material selection these components necessitate. Couplings are typically manufactured using high-strength steel alloys, carefully chosen for their resistance to corrosive environments and mechanical integrity under high-pressure conditions encountered in drilling operations.
The production processes are complex and precise, often involving heat treatment to enhance tensile strength and surface treatments to prevent corrosion. For example, one of the key processes includes phosphating, which provides a surface layer that enhances adhesion in harsh conditions. These manufacturing techniques are not just routine—each step requires expertise to ensure the final product can withstand the demanding environments of oil extraction.
api tubing couplings
Moreover, the role of non-destructive testing (NDT) in maximizing the reliability and trustworthiness of API couplings cannot be overstated. Methods such as ultrasonics, magnetic particle testing, and eddy current testing are standard in assessing the structural integrity of couplings without compromising their usability. These tests ensure that each coupling meets the rigorous quality standards required for safe operation, thereby minimizing the risk of leaks or structural failures.
Expert manufacturers often participate in third-party audits and certifications to validate the quality and performance of their API tubing couplings. These certifications provide an extra layer of trust, ensuring that end-users receive a product that has been scrutinized against potentially compromising defects.
It's also crucial to explore the innovations brought by digital technology. The integration of smart sensors and IoT technology in newer designs of API couplings allows for real-time monitoring of the coupling’s performance in situ. This ability to instantaneously gather data such as pressure and temperature changes empowers operators to make informed, timely decisions that could preempt potential failures.
Through case studies, the actual application of high-quality API tubing couplings substantiates their value. In regions characterized by extreme conditions, such as the North Sea, operators employing superior-grade API couplings report reduced unplanned maintenance and enhanced overall operational efficiency. Notably, the durability and performance of API couplings significantly contribute to minimizing the risk of environmental hazards, a critical component in preserving both ecological well-being and corporate reputation.
In conclusion, selecting the right API tubing coupling transcends mere adherence to industry standards; it reflects a commitment to operational excellence and safety. As the oil and gas industry navigates the twin challenges of maintaining productivity and reducing environmental impact, the strategic selection and application of reliable tubing couplings remain fundamental. By enrolling in continued education about the latest advancements in coupling technology and maintaining an unwavering focus on quality assurance, operators can enhance their operational resilience and sustain long-term success.