Understanding how crucial bull plugs can be in the overall structure of drilling operations is essential for anyone involved in the oil and gas industry. With extensive first-hand experience, I have seen the transformative power of high-quality bull plugs in maintaining system integrity and efficiency.
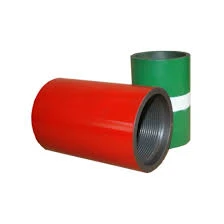
Bull plugs, a small but indispensable component, often go unnoticed yet play a significant role. They are primarily used in the drilling industry to seal off the ends of tubular sections in a pipeline or casing. This fundamental role ensures that no fluid or pressure escapes from the system, safeguarding both the equipment and the environment.
Based on years of expertise, the selection of a well-manufactured bull plug is critical. The product's material, threading, and dimensions should be scrutinized carefully to match specific operational requirements. In many instances, utilizing a stainless steel bull plug with precise threading has proven to offer durability and resistance against corrosive environments, which are common in drilling operations.

A critical factor that must not be overlooked is the expertise behind the manufacturing of the bull plug. Reputable manufacturers perform rigorous testing and adhere to international standards to ensure their products can withstand high pressure and various drilling conditions. My experience has taught me that opting for products from accredited manufacturers not only ensures compliance with safety standards but also boosts operational efficiency and reliability.
In multiple drilling projects, the use of certified bull plugs has been instrumental in averting potential leaks and structural failures. This authority on quality assurance diminishes the risk of costly downtime and repairs, reinforcing the importance of trustworthiness and reliability in product selection. The reliability offered by these products translates into enhanced safety for the crew and minimized environmental impact.
bull plug
Maintaining a comprehensive inventory of bull plugs, tailored to different sizes and materials, also aids in immediate accessibility during urgent installations or replacements. Over the years, I've witnessed how investing in a complete range of high-quality bull plugs allows for rapid adaptations to varying pressures and environmental conditions, thus maintaining uninterrupted operations.
Moreover, trust in the performance of bull plugs can be reinforced by leveraging modern technologies such as 3D scanning and predictive maintenance. By employing these techniques, potential weaknesses in the plugs can be detected early on, ensuring timely intervention and mitigating risks. This proactive approach reflects a commitment to trustworthiness and long-term cost-effectiveness, which are both valuable for any operation's sustainability.
Sharing knowledge about selecting and maintaining bull plugs should also extend to training and development programs within drilling teams. When team members understand the importance and functionality of these components, they contribute more effectively to the operation's success.
In conclusion, bull plugs may be small, but their impact on the effectiveness and safety of drilling operations is undeniably significant. By leveraging expertise, ensuring trustworthiness, and building on real-world experience, businesses can optimize their operations through the judicious selection and maintenance of these critical components. As always, prevention is better than cure – choosing the right bull plug from the outset can pave the way for success in demanding operational environments.