Bull plugs are essential components in the realm of oil and gas extraction, primarily used to seal off the end of a pipe or casing to prevent fluid loss during drilling operations. These devices are pivotal in maintaining a controlled environment within the drill string, ensuring that the procedures are conducted efficiently and safely. Drawing from extensive experience and a deep understanding of the field, this article explores the intricacies of bull plugs, emphasizing their significance, functionality, and the nuances of selecting the appropriate type for specific drilling needs.

The design of a bull plug is deceptively simple yet critically important. It typically features a threaded or non-threaded end allowing it to fit securely at the terminus of a piping setup. The effectiveness of a bull plug largely hinges on its material and construction quality. Common materials include carbon steel, stainless steel, and other high-strength alloys, chosen for their durability and resistance to harsh downhole environments. Selecting the right material for a bull plug is crucial to ensure longevity and performance under extreme temperature and pressure conditions encountered during drilling operations.
Expertise in choosing the appropriate bull plug involves understanding the specifications of the drilling project, including pressure ratings and thermal loads. For high-pressure applications, opting for a bull plug made from an alloy known for its high tensile strength and corrosion resistance is vital. This ensures the device can withstand the substantial forces exerted during operations without deforming or failing, thus maintaining the integrity of the drill string.
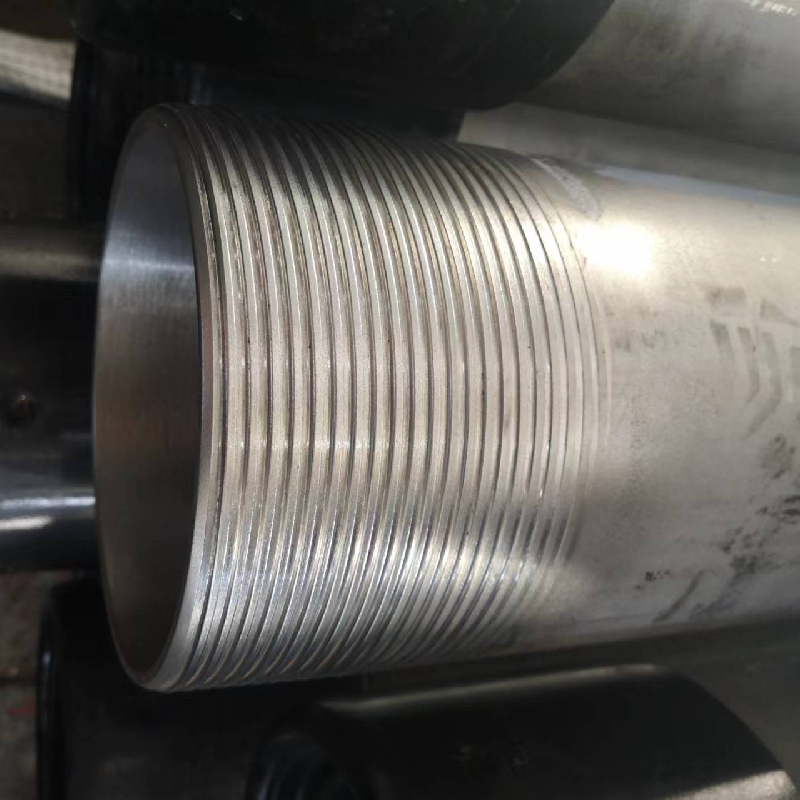
From an authoritative standpoint, adhering to industry standards and guidelines when deploying bull plugs is non-negotiable. Organizations like the American Petroleum Institute (API) establish specifications that define the manufacturing and testing parameters for these components. API certification is a marker of credibility, assuring industry professionals that a bull plug meets stringent quality and safety benchmarks.
Ensuring that these criteria are met fosters trust and minimizes the risk of operational failures.
bull plug
Another aspect of trustworthiness is the traceability and documentation accompanying the bull plug. Ensuring comprehensive documentation, including material test reports and quality certificates, aids in maintaining transparency during procurement and deployment. This traceability ensures that each component in the drilling assembly has undergone rigorous scrutiny and meets the design criteria, further bolstering confidence in the operational setup.
In practice, the introduction of advanced technologies has enhanced the performance and reliability of bull plugs. Innovations such as computer-aided design (CAD) and finite element analysis (FEA) allow engineers to simulate various down-hole scenarios, optimizing the plug’s design for maximum efficiency and durability. These technological advancements provide professionals with the tools to ascertain the ideal specifications tailored to specific drilling environments, thereby reducing the risk of unforeseen complications during operations.
For industry veterans and newcomers alike, understanding the comprehensive role played by bull plugs in oil and gas extraction culminates in optimizing drilling performance and safety. When integrated with a strategic approach that marries experience and technical expertise, these components ensure a streamlined drilling process, safeguarding against the myriad uncertainties inherent in subterranean exploration.
Thus, the indispensable nature of bull plugs in the drilling sector is underscored by their ability to enhance safety, efficiency, and reliability. By fostering a deeper understanding of their design, application, and regulatory compliance, stakeholders can make informed decisions that ultimately advance the scope and success of their drilling endeavors.