In the world of drilling and well completion, the term bull plug might not immediately spark widespread recognition, yet its significance in oilfield operations is immense. This compact yet crucial piece of equipment closes off pipe ends, effectively sealing off sections of the drill string and preserving the integrity of the well.

Navigating the application of bull plugs necessitates a deep dive into their construction, material choice, and variety of designs to match distinct operational requirements—an essential starting point for anyone invested in their utility.
Bull plugs are often crafted from stainless steel or carbon steel, renowned for their durability and resistance to corrosion. This ensures they can withstand extreme underground pressures and environmental conditions.
Professionals who work with bull plugs possess a wealth of hands-on experience, allowing them to tailor the equipment to specific scenarios. For instance, one seasoned drilling engineer recounted their team's decision to use a stainless steel bull plug in a high-salinity environment. The choice proved pivotal in preventing corrosion-related failures, mitigating downtime, and conserving resources. Such real-world experience underscores the value of bull plugs tailored to precise field conditions.
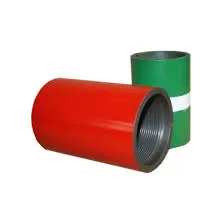
Expertise in selecting and deploying bull plugs is non-negotiable. When choosing a bull plug, engineers must consider variables such as the grade of steel, thread type, and pressure ratings. This level of detail extends beyond simple selection; it involves an understanding of the broader drilling strategy, including anticipated challenges and operational constraints.
bull plug
Authority in advocating for specific bull plug use comes from a combination of proven research and hands-on field success stories. When professionals endorse particular bull plugs, their recommendations are invariably based on a solid foundation of empirical success and industry knowledge. By centering discussions around specific case studies, such as using API-spec bull plugs in deep-sea drilling environments, one can illustrate their effectiveness and reinforce the message with factual, authoritative backing.
Trust in bull plug applications is cultivated through a transparent evaluation of their performance over time. Establishing trust means acknowledging both the successes and occasional failures encountered during high-stakes drilling operations. Sharing in-depth analyses of bull plug longevity and fault tolerance in various applications helps companies make informed choices. For example, field tests demonstrating a bull plug's performance under maximum stress conditions serve as invaluable data points for further refinement and trust-building within the industry.
In conclusion, bull plugs represent an integration of engineering expertise, real-world experience, and a demonstrative authority in their application and selection. By adhering to stringent standards and fostering a culture of trust through shared experiences and transparent data evaluations, industry professionals ensure that these seemingly modest components contribute significantly to the overall success and safety of drilling operations. Their role, while specialized, underscores a broader commitment to innovation and precision in the ever-evolving field of well completion and oil extraction.