In the intricate world of drilling and oil exploration, the importance of robust and reliable tools cannot be understated. Among these essential tools, the bull plug plays a crucial role, often overshadowed by more complex equipment. This unassuming component, however, is integral to ensuring the efficiency and safety of drilling operations.
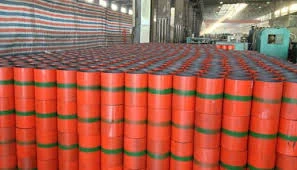
Bull plugs are essentially solid plugs used to cap off the end of a pipe. Their primary function is to close off the end of a tubular structure, thereby ensuring the integrity of the system and preventing unwanted material flow. While seeming simplistic, the expertise involved in choosing and using the right bull plug is substantial and should never be underestimated.
From the perspective of expertise, understanding the different materials of bull plugs is vital. Typically made from stainless steel, carbon steel, or other high-grade alloys, the choice of material directly impacts the plug's performance in various environmental conditions. For example, stainless steel bull plugs resist corrosion and are preferred in environments where moisture is prevalent. This material choice not only extends the lifespan of the plug but also minimizes maintenance costs, making it a cost-effective solution for operators.
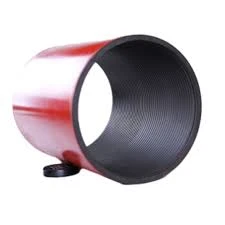
Furthermore, bull plugs are selected based on the specifications of the operation. The size, pressure rating, and threading must match the demands of the system. An ill-fitting bull plug can compromise the entire drilling operation, potentially causing leaks, system failures, or even hazardous blowouts. Thus, expertise in the precise engineering of these components underscores their efficiency and safety.
bull plug
Authoritativeness in the field of bull plugs is achieved through rigorous testing and certification. Reputable manufacturers subject their products to thorough inspections, including non-destructive testing methods such as ultrasonic testing and magnetic particle inspection. These procedures ensure that each bull plug can withstand the pressures and environmental conditions it will encounter, aligning with international standards such as ISO and API certifications. Trustworthiness is derived from this adherence to high standards, as it assures operators of the bull plug's reliability under strenuous conditions.
Real-world experiences with bull plugs reinforce their indispensability. In offshore drilling, for instance, where systems are exposed to some of the harshest environmental conditions, bull plugs have proven their worth by effectively sealing off pipe ends, thus preventing water ingress and ensuring system stability. Operators consistently report that the use of high-quality bull plugs significantly reduces the risk of operational downtime, enabling projects to proceed on schedule without costly disruptions.
Investing in quality bull plugs not only demonstrates a commitment to operational safety and efficiency but also reflects an understanding of the complexities of drilling technologies. As operations continue to expand into deeper waters and tougher terrains, the demand for reliable sealing solutions like bull plugs is set to increase. Keeping abreast with technological advancements and continuously updating equipment specifications ensures that operations remain at the forefront of industry standards.
In conclusion, while bull plugs might seem like a minor component within the broader spectrum of drilling equipment, their role is pivotal. Their design, material choice, and application directly impact the success of drilling operations. Recognizing the significance of these components, and ensuring their quality and compatibility, exemplifies a deep understanding of operational needs. Operators who prioritize such details benefit from smoother operations, reduced risks, and enhanced safety, establishing themselves as leaders in the oil and gas sector.