Bull plugs are essential components in various industries, specially designed to serve as a vital tool in well completion and maintenance processes. Renowned for their efficiency and reliability, bull plugs fulfill crucial roles in applications where sealing and pressure management are paramount. Their usage is primarily observed in oil and gas industries, where they help in ensuring the safety and efficacy of operations. Given their significance, understanding the nuances of bull plugs can greatly enhance operational outcomes and safety protocols.
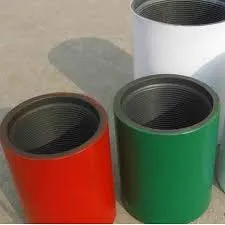
Bull plugs are typically crafted from high-strength steel or other robust materials to withstand extreme pressures and prevent leaks during critical operations. This robust construction enables them to cap off threaded pipe ends securely. In the context of oil and gas extraction, bull plugs serve as a terminating device at the end of a pipe or tubing, thus preventing fluid from flowing past the end of the pipe while allowing pressure to be maintained within the system.
In terms of expertise, professionals working in well services must be well-versed in selecting the appropriate bull plug based on specific project requirements. The choice of material, size, and thread type is fundamental, as each parameter significantly influences the efficiency and safety of oilfield operations. Steel bull plugs, for example, are often coated or treated to resist corrosion, enhancing their durability in challenging environments.
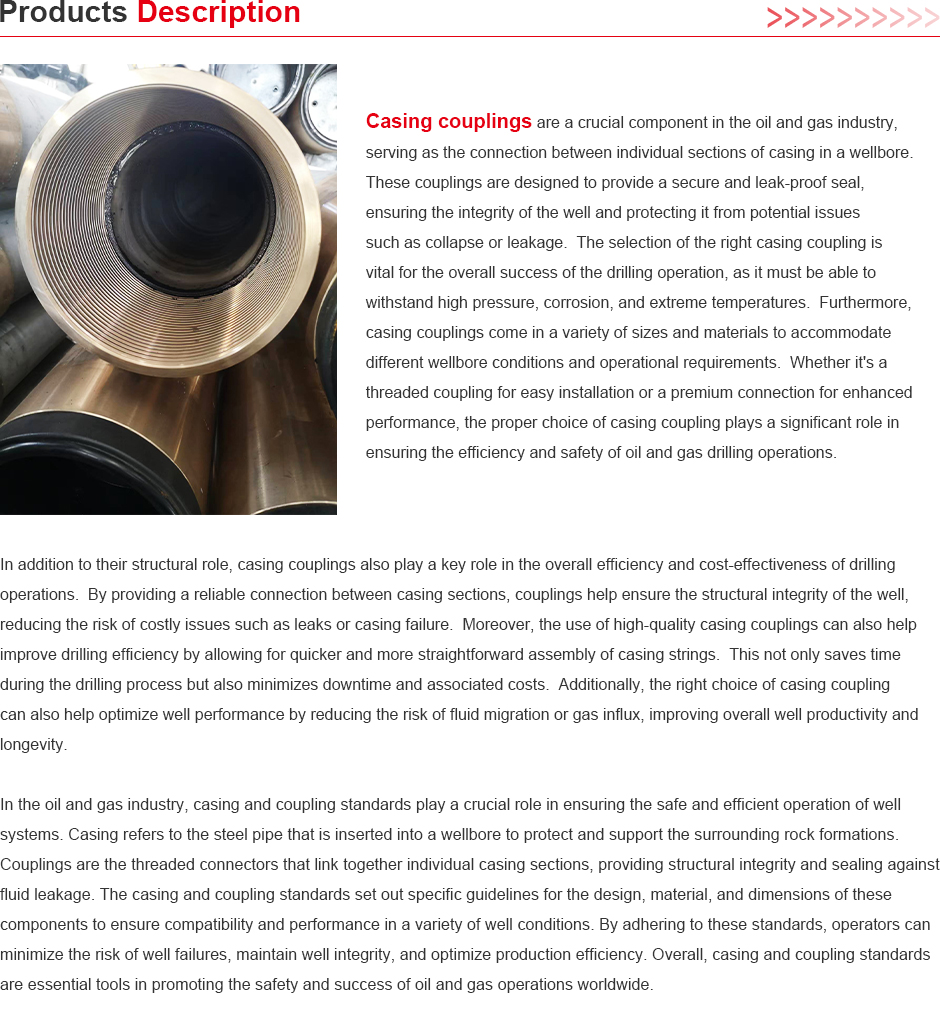
Operator experience significantly contributes to understanding the subtle operational requirements of bull plugs. Technicians are trained to recognize the specific threading patterns and ensure proper installation, thereby minimizing risks of leaks or pressure loss. Regular maintenance checks and inspections are typically recommended to prolong the lifespan of a bull plug. This practice not only assures continuing functionality but also aligns with industry standards for safety and environmental protection.
bull plug
Bull plugs are also noted for their authoritative role in pressure testing and isolation. Their ability to withstand harsh conditions without compromising integrity makes them a trusted component in wellhead maintenance. By facilitating pressure tests, bull plugs aid in verifying the system's capacity to operate under expected pressures, ensuring readiness for full-scale production. The integrity and reliability of these tests hinge on the bull plug's performance, further underscoring their critical role.
Trustworthiness in the use of bull plugs comes from adherence to stringent manufacturing standards and rigorous testing protocols. Manufacturers often conduct detailed stress testing on bull plugs to simulate real-world conditions, thereby assuring users of their functionality and reliability even under extreme duress. Documentation and certification by recognized authorities add an extra layer of credibility, offering assurance to operators regarding the safety and efficiency of these components.
In practice, the implementation of bull plugs is supported by a comprehensive understanding of well design and operational demands. Knowledge exchangep among experts and continuous training allows for the integration of innovative technologies enhancing the reliability of bull plugs. As technological advancements evolve, bull plug designs are continually refined to meet the increasing demands of deeper, more complex well structures. Innovations such as non-metallic or composite bull plugs also reflect the industry's commitment to improving efficiency while minimizing environmental impact.
In conclusion, bull plugs are an indispensable element in the toolkit of oil and gas professionals. Their role in ensuring operational safety, efficiency, and compliance with environmental regulations cannot be understated. With continuous advancements and a deep-seated understanding of well mechanics, the deployment of bull plugs remains pivotal in the sustainable and secure extraction of resources. As technological and material advancements continue to emerge, the landscape for bull plug application will advance, promising further enhancements in efficacy and safety for industry operations worldwide.