The term bull plug often appears in various industrial contexts, particularly in oil and gas, plumbing, and mechanical engineering. Yet, understanding its exact definition and applications can be quite elusive for those not directly involved in these sectors. This exploration of the bull plug aims to provide a comprehensive and insightful look into its uses, construction, and significance across industries, enhancing not only your technical knowledge but also your ability to intelligently engage with industry professionals.
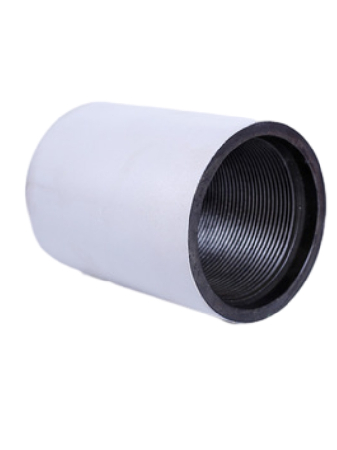
At the core,
a bull plug is a threaded pipe fitting used to close the end of a pipe. Its design typically includes a rounded, bull-nosed end that distinguishes it from other plugs. Made from metals such as stainless steel, carbon steel, or brass, bull plugs must endure high-pressure environments, making the choice of material critical. Selecting the appropriate material often depends on the specific application's pressure and temperature requirements as well as the compatibility with the fluid or gas the system transports.
In the realm of oil and gas, bull plugs play a crucial role during both well drilling and completion phases. They are often used in wellhead assemblies to seal off pressure and during various stages of downhole operations. Their ability to withstand extreme pressures makes them indispensable for maintaining safety and efficiency. Experienced engineers rely on bull plugs to ensure that segments of pipe or tubing are securely capped, thus preventing leaks and safeguarding personnel. Trustworthiness in this application is paramount; a faulty bull plug could lead to catastrophic failures, making the expertise of seasoned professionals invaluable when selecting and installing these components.
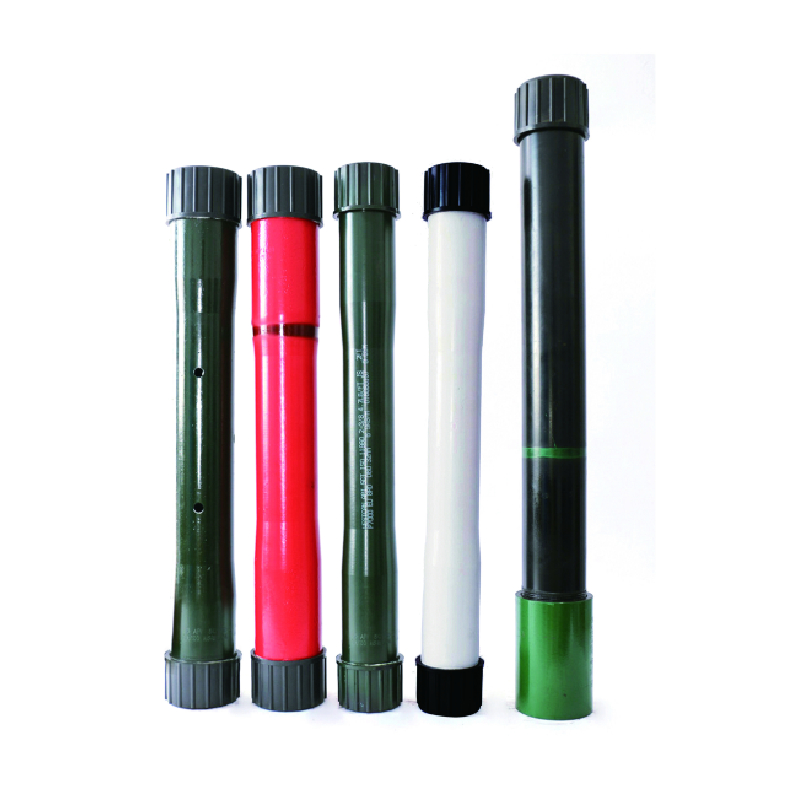
In plumbing and mechanical systems, bull plugs serve a different but no less important function. They are frequently used to temporarily seal off pipe ends in systems that are under construction or maintenance. This versatility in use showcases the bull plug's adaptability in various scenarios. Installers often praise the ease of use these fittings offer, attributed to their threaded design, which ensures a secure and tight fit. The expertise required to choose the correct thread type and size is non-negotiable, as mismatches can lead to inefficient seals and potential system failures.
bull plug definition
The authority of a bull plug in any system lies in its precision engineering and construction. Manufacturers adhere to strict industry standards and protocols to produce bull plugs that consistently perform under pressure. This reliability fosters trust among engineers and technicians who must depend on these components in diverse and challenging environments. Leading companies in this field frequently subject their bull plugs to rigorous quality assurance tests, including pressure testing, to certify their durability and performance. This commitment to quality underscores the authoritative role of bull plugs in pipe systems worldwide.
Reflecting on the real-world experiences of professionals who frequently work with bull plugs offers a wealth of practical insights. Engineers often recount tales of successfully deploying bull plugs in high-stakes environments, emphasizing the critical balance between product quality and proper installation. Their expertise illuminates the subtleties involved in selecting the right bull plug, including considerations of material compatibility, pressure rating, and thread size—factors that consistently play a role in successful applications.
In summary, the bull plug is far more than a simple pipe fitting; it is an essential component that demands expertise in selection and application. The role it plays in critical industries such as oil and gas, plumbing, and mechanical engineering underscores its importance. Professionals rely on well-designed and high-quality bull plugs for the safety, efficiency, and reliability of their systems, making it clear why these small but mighty components command respect and trust within the field.