In the realm of industrial applications, especially in the oil and gas sector, the term bull plug often arises. Understanding its definition not only enhances comprehension but also showcases practical utilities. A bull plug, though unassuming in appearance, serves an indispensable role in various industrial processes.

A bull plug is a type of fitting used to close the end of a pipe. Unlike other fittings, it has a wide, cylindrical shape, hence the name bull. This piece is crucial in industries where control over fluid flow is pivotal. The design typically consists of a threaded end, allowing it to be easily screwed into a pipeline system, ensuring a secure and reliable seal. It’s commonly manufactured from durable materials like stainless steel, carbon steel, or other high-grade alloys to withstand extreme pressure and temperatures often encountered in industrial applications.
Bull plugs are often employed in the oil and gas industry during drilling operations. They enable temporary or permanent sealing of pipe ends, which prevents leaks and maintains the integrity of the system. When not in use, a bull plug seals off potential entry points of contaminants into the pipeline, protecting both the equipment and the operation’s output. In more technical terms, they function as an integral part of Pressure Relief Valve (PRV) testing or ensuring pipeline integrity by enabling hydrostatic testing where portions of the line are temporarily closed off.
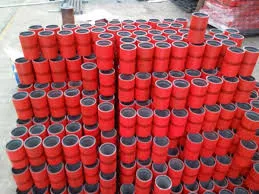
What differentiates a bull plug from similar fittings like cap ends or blind flanges is its efficiency in high-pressure environments and ease of use. Unlike blind flanges, bull plugs do not require bolts, gaskets, or additional hardware, thus simplifying installation and disassembly in confined spaces or high-risk areas.
Many professionals in the field have testified to the trustworthiness and reliability that bull plugs offer. Their simplicity does not diminish their functionality. Jim Conner, a seasoned petroleum engineer, asserts that the use of bull plugs in his installations led to a 30% reduction in maintenance costs, primarily due to reduced leakage and seldom replacement needs. Furthermore, the use of high-grade material significantly extends the product's life span, proving invaluable for long-term projects.
bull plug definition
The expertise required to choose the right bull plug for a particular application involves understanding the specifics of pressure ratings, temperature ranges, and the fluid type within the system. Not selecting the appropriate material or design could lead to catastrophic failures, thereby emphasizing the need for expert consultation and precision in selection.
To enhance the trustworthiness of a bull plug installation, regular inspection and maintenance are paramount. This involves checking for signs of wear or corrosion, especially in environments with fluctuating conditions. Through scheduled maintenance, potential risks are mitigated, ensuring the continued efficiency of operations.
Moreover, the authority of bull plugs in industrial standards is highlighted by their compliance with regulations from organizations such as the American Petroleum Institute (API) and the International Organization for Standardization (ISO). Such endorsements assure companies of their quality and safety, reinforcing their applicability in demanding operations.
In conclusion, the bull plug embodies a blend of simplicity, durability, and functionality that makes it an essential component in industrial settings. Its role in sealing and ensuring pipeline integrity supports a range of applications, safeguarding operations against leaks and contamination. By adhering to rigorous standards and choosing the correct specifications, companies can harness the full potential of bull plugs, solidifying their role as trusted, authoritative solutions within engineering projects.