Understanding the precise dimensions and specifications of bull plugs is crucial for industry professionals seeking to optimize their equipment and processes. A bull plug is typically used in the oil and gas industry to seal off pressure, terminate a line, or perform testing. To ensure seamless operations, understanding the variability in dimensions and their applications is essential.

Bull plugs come in a variety of sizes and configurations, each designed for specific usage. Generally, they are machined from solid metal, ensuring durability and reliability under high-pressure environments. The most common materials used include stainless steel, carbon steel, and alloys, chosen for their strength and resistance to corrosion. The actual dimensions of a bull plug can significantly impact its functionality, making it vital for operators to choose the correct specification for their needs.
The length of a bull plug can vary, typically ranging from a few inches to several feet. Alongside length, another crucial dimension is the outer diameter, which must match the dimensions of the pipe or fitting it is intended for. These components often come in sizes ranging from 1/8 inch to several inches in diameter, allowing compatibility across various systems. Additionally, threading is another key aspect, usually adhering to NPT (National Pipe Thread) standards in the USA, ensuring a secure and leak-proof fit.
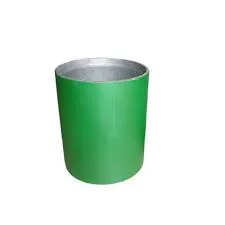
Operators must also consider the bull plug's pressure rating. High-quality products often withstand pressures upwards of several thousand PSI, which is vital for high-pressure applications encountered in oil and gas extraction. When selecting a bull plug, verifying the pressure rating against expected operating pressures is critical to prevent equipment failure or safety hazards.
In terms of expertise, understanding the trade-offs between different materials used in bull plug manufacturing is pivotal. Stainless steel bull plugs are renowned for their corrosion resistance, making them suitable for offshore and subsea applications. Carbon steel variants are cost-effective and provide substantial strength, suitable for onshore operations where corrosion may be less of a concern. Alloy bull plugs offer enhanced mechanical properties and are often used in challenging environments that demand superior performance.
bull plug dimensions
The criticality of precise bull plug dimensions isn't limited to fluid and gas handling. Specialists in the field often rely on industry standards and regulatory guidelines to ensure compliance and safety. Using the incorrect dimensions can result in workflow disruptions, safety incidents, and increased operational costs. Consequently, many professionals turn to established manufacturers known for their commitment to quality and precision.
For those delving into the selection or usage of bull plugs, consulting with a certified engineer or supplier can provide additional peace of mind. Their expertise can guide the selection process, ensuring that each bull plug meets the specific demands of the job. Moreover, they can offer insights into custom solutions when standard sizes and materials are insufficient for certain applications.
Authoritativeness within the industry often stems from consistent performance and reliability of the components used, backed by compliance with global standards such as ISO and API. Companies that invest in high-quality bull plugs not only ensure the safety and efficiency of their operations but also gain a competitive edge through minimal downtime and enhanced productivity.
Trust in these components is further built through supplier reputation and documented performance histories, which help in building long-term partnerships in resource extraction industries. Reliable suppliers are usually transparent about the performance tests their bull plugs undergo, adding an extra layer of confidence for the purchasers.
In conclusion, the dimensions of bull plugs, along with their material composition and pressure ratings, are fundamental to their successful application in the industry. By combining technical knowledge with industry standards, operators can ensure not only operational safety but also improved performance and cost efficiency. It is the amalgamation of experience, expertise, authoritativeness, and trust that ultimately guides the successful implementation of bull plug dimensions in high-stakes environments.