Bull plugs, though often overlooked, are an essential component in the toolkit of any oil and gas drilling operation. These simple yet effective devices serve a critical function—sealing the end of a pipeline to prevent fluid loss. Understanding the dimensions and intricacies of bull plugs is crucial for anyone involved in the design, selection, and application of these tools in the field.
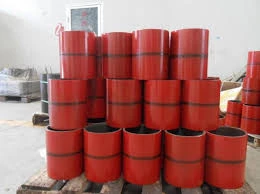
Bull plugs come in an array of sizes and configurations, aligning with the varied demands of industrial applications. They are manufactured to fit specific pipeline measurements, ensuring a secure fit and optimal performance. When selecting the appropriate bull plug, one must consider not only the diameter of the pipeline but also the pressure requirements, material compatibility, and environmental conditions.
Expertise in bull plug dimensions begins with recognizing the standard sizing conventions used in the industry. Typically, bull plugs are designated by the diameter of their threading connection, with common sizes ranging from 1/8 inch to several inches in diameter. The selection process involves matching the bull plug’s threads to those of the pipeline,
ensuring a seamless seal. Furthermore, dimensions also encompass the length of the plug, which should be sufficient to accommodate the application’s needs without risking over-penetration or inadequate coverage.
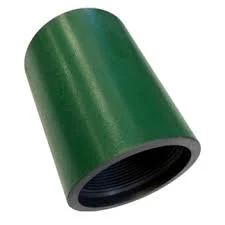
Authoritativeness in this field is underscored by adhering to industry standards and regulations. API (American Petroleum Institute) specifications provide detailed guidelines for the manufacturing and sizing of bull plugs. Compliance with these standards assures that the bull plugs will perform under the specified conditions, maintaining integrity even under high-pressure scenarios. Additionally, some manufacturers offer customizable options to cater to unique operational requirements that might fall outside standard dimensions.
Products made from different materials may vary slightly in terms of dimensions and performance. Common materials include carbon steel, stainless steel, and exotic alloys, each offering distinct advantages in terms of strength, corrosion resistance, and temperature tolerance. For operations in corrosive environments, stainless steel or specialized coatings may be preferable, while carbon steel is often chosen for its combination of strength and cost-effectiveness in less demanding settings.
bull plug dimensions
The expertise of seasoned engineers and technicians plays a critical role in assessing the impact of these factors on the bull plug’s dimensions. They examine the operational environment, considering temperature extremes, chemical exposure, and mechanical stresses, before recommending the most suitable bull plug specifications. Proper sizing ensures not only that the plug fits the pipeline but also that it withstands operational pressures and resistances, contributing to the reliability and efficiency of the overall system.
Real-world experience in the application of bull plugs further reinforces the importance of accurate measurements and quality materials. From offshore drilling platforms subjected to saltwater corrosion to onshore systems handling high-sulfur crude oils, each scenario requires a tailored approach to bull plug selection. Field data, collected through rigorous testing and observation, guides ongoing improvements in bull plug design and material selection, enhancing performance and lifespan.
In practice, trustworthiness in bull plug applications is demonstrated through thorough testing and certification processes. Manufacturers invest in extensive quality control measures, subjecting their products to pressure testing, material analysis, and dimensional verification. These processes are documented meticulously, providing customers with the assurance that every bull plug meets or exceeds the necessary specifications.
For professionals in the oil and gas sector, staying informed about the latest advancements in bull plug technology and materials is crucial for maintaining a competitive edge. Continuous education, industry conferences, and technical publications serve as valuable resources for learning about innovative solutions and best practices in the field.
In summary, bull plugs are indispensable components that necessitate careful consideration of dimensions, materials, and application conditions. Expertise and authority in the industry are achieved through a commitment to quality, adherence to standards, and integration of field experience. As the energy industry evolves, the demand for highly reliable, performance-oriented bull plugs continues to grow, underscoring their role in sustainable and efficient resource extraction.