Bull plug pipe fittings may not be the most discussed component in the vast world of plumbing and pipeline engineering, yet their significance cannot be underestimated. As an understated yet indispensable part of many industrial setups, understanding their applications, materials, and installation processes is vital for both engineers and field workers.
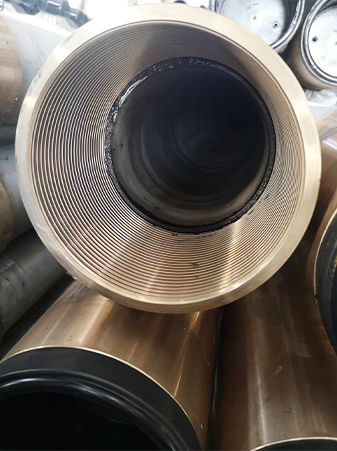
Similar to the role of a conductor in an orchestra, bull plug pipe fittings ensure that systems operate smoothly without unnecessary interruptions. These fittings are primarily used for sealing the end of a pipeline or connection, which might otherwise expose the system to potential leaks or contamination. Their role is universal across industries, whether it’s in oil and gas, wastewater management, or chemical processing.
From a material standpoint, bull plug pipe fittings are manufactured using a range of metals, with carbon steel, stainless steel, and alloy steel being the most common. The choice of material directly corresponds to the specific environment in which they are utilized. For instance, in high-pressure environments often encountered in oil rigs, high-strength alloy steel bull plugs are preferred due to their robustness and resistance to extreme pressures and temperatures.
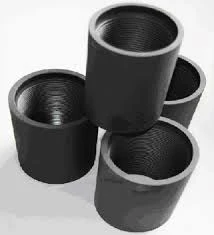
Installation of these fittings demands a precise approach. Improper installation can lead to system failures, which might result in environmental hazards or financial losses for businesses. Thus, collaboration with certified professionals who possess considerable expertise is crucial. They ensure that the fitting not only matches the threading and pressure requirements but is also compatible with the fluid or gas being transported.
bull plug pipe fitting
The trustworthiness of a bull plug's design and manufacturing is paramount. It is essential to source these fittings from manufacturers that adhere to international quality standards such as ASTM and ASME. Companies that invest in rigorous testing methods, including hydrostatic and ultrasonic testing, often provide an extra layer of assurance regarding the product’s integrity and performance under stress.
Expertise in the field of bull plug usage can prevent misapplications that might otherwise compromise system integrity. For example, selecting a bull plug with incompatible material or ratings can introduce vulnerabilities, impacting both safety and efficiency. Hence, professionals keen on advancing their understanding should engage with continued education opportunities and technical workshops to remain current with industry innovations and standards.
Experience is not just a desirable trait but a necessity when dealing with bull plug installations. Seasoned professionals draw from an extensive background of past projects, thereby enhancing their capability to troubleshoot unexpected onsite challenges effectively. This seasoned insight is invaluable, reducing downtime and ensuring that the pipeline systems remain operational without unforeseen interruptions.
In conclusion, while bull plug pipe fittings might not attract the same attention as other components, their contribution to the seamless functioning of pipeline systems is undeniable. Through a combination of expert knowledge, reliable sourcing, and practical experience, professionals can maximize the performance and safety of these essential fittings, guaranteeing long-term functionality and trustworthiness for their clients.