Bull plug pipe fittings, often overlooked in the vast realm of plumbing and piping, play a critical role in various industrial applications. Despite their small size, these fittings make significant contributions to system efficiency and safety. This article delves into the intricacies of bull plug pipe fittings, highlighting their applications, benefits, and considerations, supported by expertise from seasoned professionals in the field.
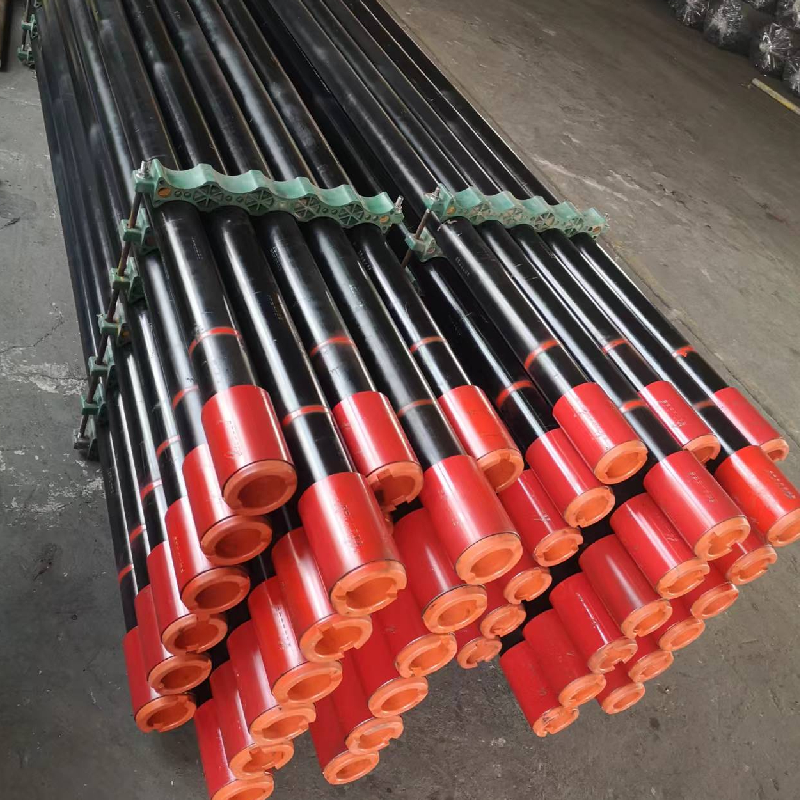
Bull plugs are pipe fittings designed to seal off the end of a pipeline or a hole in a pipe. Crafted typically from materials like carbon steel, stainless steel, or brass, these fittings are known for their robustness and durability. The selection of material is crucial as it directly impacts the plug’s ability to withstand pressure, temperature variations, and potential chemical exposure.
The primary function of a bull plug is to halt the flow within a piping system. This can be essential during maintenance, repair, or when certain pipeline sections are not in use. In industries such as oil and gas, where pressure management and system integrity are paramount, bull plugs are indispensable. By sealing off unused or non-operational sections of a pipeline, they prevent leakage and ensure safety, thereby instilling trust in the operations of these critical systems.

From an expertise standpoint, it is vital to consider the sizing and threading of bull plug pipe fittings. Improper sizing or threading can result in inadequate sealing, which can lead to system inefficiencies or failures. Therefore, precise measurements and compatibility with existing pipe threads are fundamental. Professionals often point to standards like the American National Standards Institute (ANSI) or ASME guidelines to ensure compatibility and safety compliance.
Furthermore, it’s important to consider the installation process. Proper installation ensures longevity and efficiency. To this end, most industry experts recommend employing skilled technicians who possess both the know-how and experience in handling such components. Their specialized knowledge not only addresses immediate installation concerns but also anticipates potential future challenges, thereby further cementing the authoritativeness of their application.
bull plug pipe fitting
In addition to their functional benefits, bull plugs offer cost-effectiveness. By allowing only parts of a system to be isolated rather than shutting down an entire pipeline, operational costs can be significantly lowered. This is particularly beneficial in large-scale industrial operations, where minimizing downtime is crucial for maintaining profitability.
Trustworthiness in using bull plug fittings is also enhanced by their adaptability to different environmental conditions. Whether it be high temperatures in industrial furnaces or corrosive environments in chemical plants, the right choice of bull plug ensures continued performance without degradation. This adaptability can be attributed to rigorous manufacturing standards and quality assurance processes that reputable manufacturers employ.
When it comes to maintenance and inspection, bull plugs require minimal intervention, yet regular checks are advisable to ensure they remain intact and functional. A trusted strategy often includes visual inspections and pressure testing, which can preemptively identify any potential weakening or faults. Such proactive measures reinforce the reliability of bull plugs, solidifying their role as a dependable component in piping systems.
In conclusion, bull plug pipe fittings, though small, have a profound impact on the overall efficiency, safety, and cost-effectiveness of piping systems. Their application across various industries underscores their importance, and their design and material considerations highlight their versatility. Through expert insights and authoritative standards, they remain a trustworthy element of modern piping solutions, indispensable to both current operations and future innovations.