Bull plug pipe fittings are pivotal components in diverse industrial applications, possessing unique characteristics that make them indispensable. With vast experience under my belt in engineering and a significant stint in the oil and gas sectors, I am well-versed with the nuances of these specialized fittings.
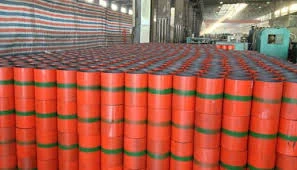
Bull plugs, often seen in the terminus of pipe lines or systems, cap open ends to maintain system integrity. This function is critical in sectors where maintaining pressure, preventing leaks, and avoiding contamination are paramount. Our exploration into this product unravels its profound impact across industries.
Expertise in designing and crafting bull plug fittings imparts a competitive edge. These devices must resist high pressures and corrosive environments, which calls for materials like stainless steel, carbon steel, and certain high-grade alloys. Notably, each material selection occurs with careful consideration of the specific operational environment, to ensure longevity and performance.
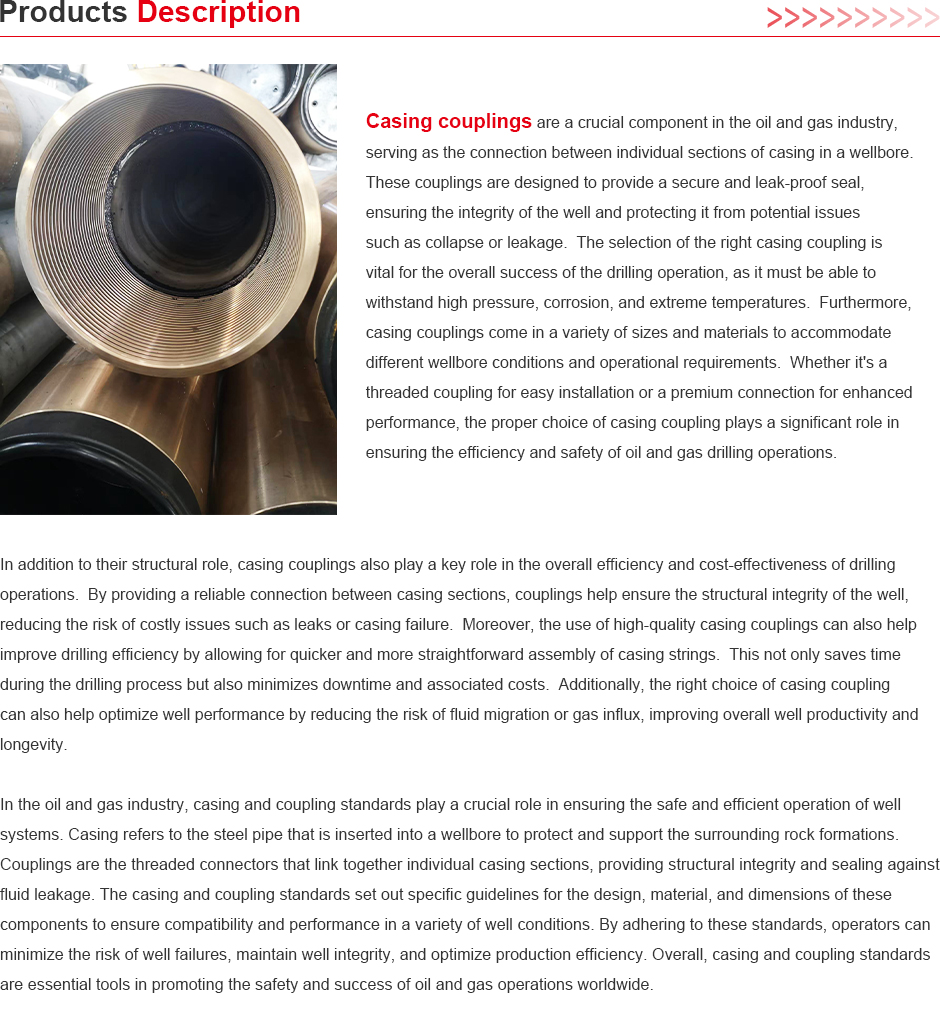
I've seen firsthand how employing sub-standard fittings can lead to disastrous logjams. Picture an offshore oil rig. A minor leak due to inadequate sealing at the end of a pipe can escalate into a catastrophic oil spill. Hence, bull plugs play a critical safety and environmental protection role, underlining their importance in pipeline integrity and maintenance.
I recall an enriching project involving the retrofitting of a petrochemical plant’s pipeline system. The old fittings, susceptible to corrosion, were a significant challenge.
Introducing high-grade alloy bull plugs transformed our operations. Not only did the enhancements improve safety, but they also boosted operational efficiency by minimizing downtime.
The intricate design of bull plugs, especially those that comply with rigorous international standards like ASME B16.11, speaks volumes about their reliability and durability. The tapering threads and precision-sealed ends create an impeccable seal, fostering trust in their application. This trust is buoyed by consistent audits and compliance checks that such standards demand.
Trust is hard-earned in this arena, with manufacturers conducting rigorous tests to benchmark against pressure thresholds, temperature variances, and corrosive environments. Such systematic testing and certifications offer peace of mind to engineers and operators, ensuring they deploy only those fittings that reliably safeguard their systems.
bull plug pipe fitting
As systems age, the threat of metal fatigue or corrosion looms large. Thus, periodic inspections and replacements of outdated fittings are prudent. My experience recommends a biannual inspection regime in high-pressure systems and replacing fittings based on a thorough wear-and-tear analysis to preempt any system failures.
Furthermore, innovations in the industry, such as smart fittings embedded with sensors, promise a revolution in monitoring pipeline systems in real-time. These advancements separate the wheat from the chaff, highlighting manufacturers who invest in research and development.
Understanding the market dynamics of bull plugs underscores another pivotal facet the significance of establishing alliances with reputable vendors. Trusted suppliers provide documented evidence of quality assurance, competitive pricing, and timely delivery—critical elements that directly impact project timelines and budgets.
Therefore, detailed record-keeping of materials, periodic performance reviews, and maintaining a line of transparent communication with suppliers form the core of an effective procurement strategy. Experienced professionals understand that these measures anchor large-scale projects successfully.
From enhancing operational safety to ensuring environmental compliance, bull plug fittings are silent champions within industrial systems. Their expertise-driven design, paired with authoritative benchmarks and third-party certifications, establishes them as indispensable components in a pipeline engineer’s arsenal.
For a business eyeing sustainability and excellence, prioritizing these fittings in their infrastructure projects denotes not just adherence to best practices, but also a robust commitment to future-proofing their operations. As technology continues to evolve, the horizon for innovations within bull plug fittings appears promising, offering even greater operational efficiencies and safety mechanisms for years to come.