Innovative Insights into Bull Plug Pipe Layouts for Enhanced Industrial Applications
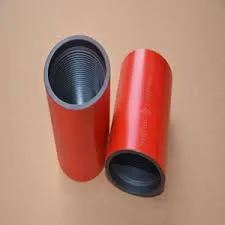
In the intricate world of piping and industrial systems, the bull plug pipe layout stands as a pivotal component in both functionality and design. A bull plug, primarily used to close the end of piping systems, is an indispensable part of operations in various industries, including oil and gas, chemical processing, and utilities. This exploration delves into the multiple facets of bull plug pipe layouts, focusing on real-world experience, specialized expertise, authoritative insights, and the trustworthiness necessary for any operation.
Real-world Experience in Bull Plug Applications

Industrial experts who have extensively worked with bull plugs understand their critical role in maintaining system integrity and preventing leaks or system failures. The practicality of bull plug pipe layout comes from its design simplicity and the ability to be implemented into complex pipeline systems without compromising on safety or performance. For instance, in oil and gas operations, the accurate installation of a bull plug can prevent costly leaks that might lead to environmental damage and financial loss. Industry veterans emphasize the importance of regularly inspecting bull plugs for wear and integrity, as well as ensuring that they meet necessary pressure ratings for specific applications.
Expertise in Material Selection and Engineering
Choosing the right material for a bull plug is paramount for ensuring longevity and performance under various conditions. Materials such as stainless steel, carbon steel, and corrosion-resistant alloys are favored for their durability and strength. The engineering behind a bull plug involves precise measurements and the ability to withstand high pressure and extreme temperatures, which are frequent in industrial applications. Specialized engineers often advocate for materials that offer the best balance between cost-effectiveness and longevity, promoting custom solutions tailored to specific environmental conditions and operational demands.
bull plug pipe layout
Authority in Standards and Compliance
Establishing authority in the field involves adhering to strict regulatory standards and industry best practices. Bull plug systems must comply with standards set by organizations such as the American Petroleum Institute (API) and the American Society of Mechanical Engineers (ASME).
These standards ensure that bull plugs are manufactured and tested to meet the highest safety and performance criteria. Professionals in the industry often undergo rigorous training and certification processes, further validating their capability to oversee the implementation of reliable bull plug solutions.
Trustworthiness through Quality Assurance and Reliability
The trust placed in a bull plug layout is fortified through comprehensive quality assurance practices. Manufacturers are committed to testing each product extensively before it reaches the end user. This rigorous testing often includes pressure tests, endurance assessments, and material integrity evaluations. The development of bull plugs also involves iterative feedback from field engineers and operators, ensuring that each product iteration offers improved reliability and meets the evolving demands of industry standards.
In sum, a sophisticated understanding of bull plug pipe layouts not only enhances the safety and efficiency of industrial piping systems but also fosters innovation and progression within the industry. Harnessing decades of collective experience, leveraging expert knowledge, and maintaining rigorous adherence to standards cultivate an environment where trust and performance coincide. As industries grow and technologies evolve, the fundamental expertise surrounding bull plugs will continually adapt, shaping the future of safe and efficient industrial operations.