Bull plug pipes, essential components in the oil and gas industry, are designed to seal pipe ends, especially in high-pressure conditions. Understanding the nuances of bull plug pipe layouts can significantly impact both efficiency and safety in drilling operations. These devices, often overshadowed by more extensive components, play a critical role that underscores the importance of their strategic application and integration.
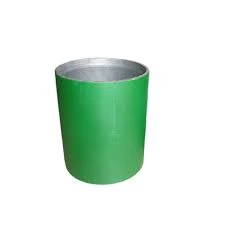
Drawing from years of field experience, the optimal layout design of bull plug pipes can enhance their functionality and longevity. A typical bull plug pipe layout will incorporate a strategic arrangement that facilitates prompt access and ease of maintenance. Such a layout will factor in the operational requirements, environmental conditions, and specific industry standards.
In terms of expertise,
selecting the right material and dimensions for bull plug pipes is paramount. Carbon steel and stainless steel are frequently chosen based on their pressure ratings and resistance to environmental factors like corrosion. However, the emerging trends suggest an increasing reliance on advanced composite materials that offer superior strength-weight ratios and enhanced durability. The proper alignment and connection techniques can prevent mishaps and ensure that the piping system operates without unnecessary strain or pressure drop, which could otherwise lead to catastrophic failures.
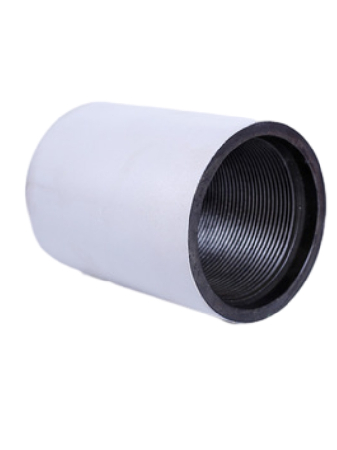
bull plug pipe layout
From an authoritative standpoint, the adherence to industrial standards, such as those outlined by the American Petroleum Institute (API), is non-negotiable. Ensuring that the bull plug pipes and layouts meet these standards not only maximizes system integrity but also complies with regulatory safety norms. Incorporating pressure test procedures, such as hydrostatic testing, can further ascertain the reliability of these devices under extreme conditions, thereby reinforcing their credibility within high-stakes operational settings.
Building trust in bull plug pipe systems also derives from transparent sourcing and certification of materials. Partnering with verified suppliers who provide documentation and traceability for their materials assures clients of product authenticity and conformance to standards. Regular audits and updates of the system layout, conducted by experienced professionals, can prevent oversight and maintain operational security.
In conclusion, advanced understanding and strategic implementation of bull plug pipe layouts contribute immensely to the success of oil and gas extraction operations. By leveraging expertise in material choice and layout design, aligning with authoritative standards, and ensuring trust through rigorous quality checks, businesses can optimize their pipe systems for performance and safety. Such informed approaches not only enhance operational efficiency but also safeguard against potential risks, providing a robust foundation for sustained industry success.