Understanding the intricacies of bull plug pressure ratings is pivotal for professionals in industries such as oil and gas, where these components play a crucial role in maintaining the integrity and safety of well operations. Bull plugs, known for closing off pipes, are essentially steel fittings that cap the end of the line, preventing the escape of fluids and maintaining pressure within the pipeline system. The importance of their pressure ratings cannot be understated, as they determine the conditions under which this equipment can safely operate, ensuring both operational efficiency and safety compliance.

When selecting bull plugs for industrial applications,
expertise in their pressure rating is essential. Pressure ratings indicate the maximum pressure that the bull plug can withstand without risk of failure. These ratings are typically expressed in pounds per square inch (PSI), guiding engineers and technicians in selecting components that match or exceed the pressure demands of the system. Selecting a bull plug with an appropriate pressure rating mitigates the risk of system failures, which can lead to costly downtime or even catastrophic accidents, emphasizing the importance of precision in this selection process.
Real-world experience demonstrates that understanding the material composition and design standards of a bull plug is crucial for determining its pressure rating. Bull plugs are typically manufactured from high-strength steel, designed to withstand the intense pressures found within industrial systems. Standards set by organizations like the American Society for Testing and Materials (ASTM) ensure that these components can cope with specific conditions, factoring in aspects like temperature extremes and corrosive substances. An experienced engineer, equipped with this knowledge, is thus empowered to make informed decisions that uphold safety and efficiency.
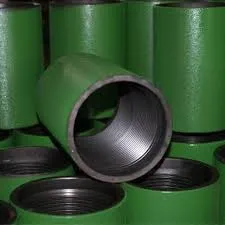
In practical terms, the expertise surrounding bull plug pressure ratings involves consideration of not only static pressure but also dynamic conditions such as pressure surges. A trusted source will emphasize that pressure surges, which occur when the flow of media within the pipeline is abruptly changed, can exert pressure levels higher than those normally encountered. Engineers, with their specialized knowledge, thus design systems to accommodate these surges, providing an additional safety buffer beyond the stated pressure rating of the bull plug.
bull plug pressure rating
Authoritativeness and trustworthiness in the field of pressure containment begin with reliance on reputable manufacturers and suppliers. Purchasing bull plugs from companies with a history of adhering to stringent quality standards reassures stakeholders of the component's reliability. These companies typically offer comprehensive documentation, including pressure rating certifications, performance data, and compliance with regulatory standards, such as API (American Petroleum Institute) specifications. Such transparency is a hallmark of a trustworthy supplier, assuring clients of product authenticity and performance fidelity.
For stakeholders aiming to maintain operational safety and efficiency, regular inspection and maintenance are advised. Ensuring that bull plugs remain within their pressure specifications over time involves routine checks for signs of wear or corrosion, especially in harsh environments. Expert recommendations often extend to advanced techniques like non-destructive testing methods, which can provide a deeper insight into the component’s integrity without compromising its usability.
Ultimately, determining the appropriate bull plug pressure rating is a detailed process involving a balance of informed material selection, system design considerations, and ongoing maintenance protocols. For industry leaders aiming to enhance their practices, the integration of authoritative guidelines, expert insights, and hands-on experience forms the bedrock of successful operational management, all while keeping safety and performance at the forefront. Investing in expertise and understanding around pressure ratings is not merely a technical necessity but a strategic pillar supporting sustainable, safe, and efficient operational foundations.