Bull plugs, though a niche component, play an essential role in the oil and gas industry by ensuring operational safety and equipment integrity. With the increasing demand for efficient and safe drilling operations, understanding the attributes and applications of bull plugs has become more pertinent than ever before.
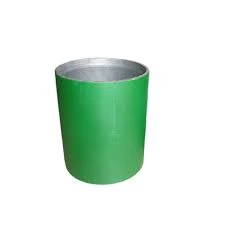
At their core, bull plugs are threaded pipe fittings typically used to close the end of a pipe. Their design is crucial because they provide a secure end to piping systems, ensuring no leakage or unintended flow, which could lead to operational hazards. In industries where pressurized fluids are handled, the role of these components becomes even more significant.
One of the most significant benefits of bull plugs is their contribution to maintaining system integrity under high pressure. Failure of any piping component in this setting can lead to substantial negative consequences, not just in equipment damage, but in serious safety hazards. Therefore,
selecting a reliable bull plug is vital. Investing in high-quality bull plugs, made from robust materials like stainless steel or high-grade alloys, is a prudent choice to ensure longevity and reliability. Brands known for adhering to API standards (American Petroleum Institute) are typically trusted partners in this space.
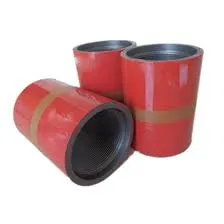
When it comes to the expertise involved in utilizing bull plugs, choosing the right size and threading is key. A mismatch can result in poor fits, potential leakages, and compromised safety. Industry professionals recommend having a comprehensive understanding of the threading types, such as NPT (National Pipe Tapered) and API connections, to ensure compatibility with existing systems. Additionally, ensuring that operators are trained in the installation and maintenance of bull plugs is essential for seamless operations.
It's not merely product specifications that demonstrate expertise, but the real-world experience of those on the ground using these products daily. Seasoned professionals often share anecdotes where the right choice of bull plug prevented potential disasters. In some documented instances, operators have encountered unexpected pressure spikes in pipelines; high-quality bull plugs were the unsung heroes that withheld these spikes without fail.
bull plugs
Choosing bull plugs with the right surface finishing and thread lubrication can further optimize system performance. A smooth finish reduces friction during installation, while proper lubrication prevents galling—a common issue where metals cold-weld under pressure. Trustworthy suppliers will provide these added features, ensuring the product performs beyond simple expectations.
Trustworthiness in this niche market doesn’t stem from eloquent marketing but from consistent performance and third-party validation. Operators should seek bull plugs with certifications and endorsements from recognized bodies in the industry. Peer reviews, especially those from established industry professionals, offer invaluable insights into real-world performance, shedding light on any limitations a product might have. It's crucial to tap into industry networks and forums where these reviews and experiences are regularly shared.
Nonetheless, while bull plugs might seem like a small aspect of a broader system, it’s vital to understand their impact on an operation's overall safety and efficiency. Missteps in selection or installation can lead to downtime and increased operational costs, not to mention the safety risks involved. Therefore, maintaining a stringent selection process for your bull plugs, working closely with trusted suppliers, and leaning on the collective knowledge and experiences within the industry will position any operation favorably.
In summary, the journey to mastering the use of bull plugs involves more than just technical know-how. It encompasses a dedication to quality, a commitment to operational best practices, and a reliance on shared industry knowledge. Keeping these factors in focus ensures that bull plugs will serve their purpose effectively, securing the integrity of critical piping systems across the world’s most demanding industrial landscapes.