When comparing bull plugs and hex plugs, the distinction extends beyond mere aesthetics or simple functionality. These two types of plugs serve pivotal roles in various industries, particularly within oil and gas, mechanical, and plumbing sectors. Their design, application, and performance characteristics influence their usage, and understanding these nuances can enhance operational efficiencies and safety.
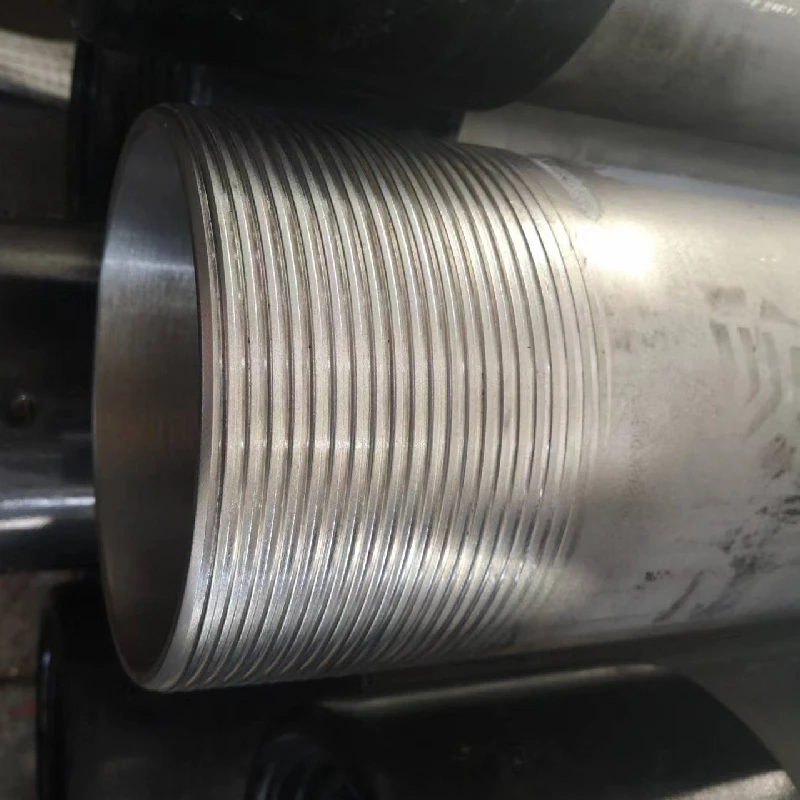
Bull Plug Heft and Solidity in Design
Bull plugs are a staple in the oil and gas industry, primarily used to seal the end of a pipe. Typically employed in situations calling for temporary sealing, bull plugs are renowned for their rounded or blunt end. This design helps minimize damage to other pipe components during installation or removal. Constructed from robust materials such as stainless steel or carbon steel, they deliver high pressure and temperature resistance, making them ideal for harsh environmental conditions often encountered in drilling operations.
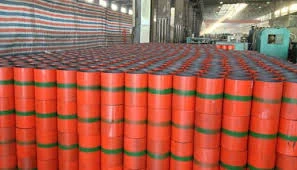
One of the notable benefits of using bull plugs is their versatility. They cater to both the upstream and downstream sectors of oil and gas operations. In upstream activities, bull plugs might cap off high-pressure lines during pressure testing or maintenance. In downstream contexts, they ensure that inactive lines are secured efficiently, minimizing the risk of leaks or accidents.
However, it’s essential to choose the appropriate bull plug size and material based on specific operation requirements. Selecting an undersized plug may lead to insufficient sealing, whereas oversized plugs can result in undue stress on the pipe, leading to potential failures.
Hex Plug Precision and Practicality
Hex plugs, characterized by their hexagonal heads, are frequently used in plumbing and pneumatic applications. Their design allows for easy installation and removal using a wrench, which facilitates maintenance tasks. Hex plugs often seal off threads and tapped holes, offering a secure and reliable solution for preventing fluid leaks.
Material choice for hex plugs typically includes brass, stainless steel, and nylon, each offering unique benefits. Brass plugs are favored for their corrosion resistance, making them suitable for water applications. Stainless steel variants provide strength and a tolerable degree of corrosion resistance, ideal for more industrial applications, while nylon plugs are lightweight and rustproof, albeit suitable for less demanding scenarios.
bull plug vs hex plug
The role of hex plugs can’t be overstated in precision applications. Their ability to be tightened to exact specifications ensures that each connection remains secure, a critical requirement in high-precision industries such as aerospace and automotive manufacturing. The hexagonal design also allows for easy application of torque, reducing the risk of damage to the plug or surrounding components.
Comparative Dynamics Choosing the Right Plug
The decision to use a bull plug versus a hex plug encapsulates more than just fitting needs; it involves a strategic assessment of operational conditions and requirements. When faced with volatile pressure environments or large-scale industrial applications, the bull plug stands out due to its durability and ability to withstand harsh conditions. In environments where ease of installation and removal are of essence, coupled with moderate operational demands, hex plugs offer a compelling choice due to their ergonomics and sealing capabilities.
Operational safety and functionality should prioritize material integrity and dimensional accuracy. Both bull and hex plugs should meet industry standards and undergo rigorous testing to ensure performance reliability. Moreover, regular maintenance, involving inspections and possible replacements, is crucial to preserving the integrity of systems in which these plugs are implemented.
Future Considerations and Innovations
In the face of advancing technology, both bull plugs and hex plugs have undergone significant evolution to meet the increasing demands of modern industrial applications. Innovations in material science have led to the development of composite materials offering enhanced strength and reduced weight. Smart plugs equipped with sensors to monitor pressure, temperature, and other parameters in real-time are becoming more mainstream, driving predictive maintenance practices and reducing downtime.
As industry dynamics continue to shift, especially with the rise of automation and IoT technologies, the role of these plug types will undoubtedly expand. Companies investing in next-generation plug solutions not only improve operational efficiencies but also position themselves as leaders in sustainable and safe industrial practices.
In summation, both bull plugs and hex plugs possess distinct attributes making them indispensable across various industries. Understanding their unique characteristics, coupled with thoughtful integration into system design, can optimize performance, ensure safety, and ultimately lead to operational excellence.