The landscape of well completion technology is vast and ever-evolving. Among the many components essential in the drilling and completion of oil and gas wells, bull plugs and round head plugs stand out for their distinct functionalities and applications. In an industry where every decision can impact efficiency, cost, and safety, understanding the differences between these two types of plugs is critical for engineers and operators.
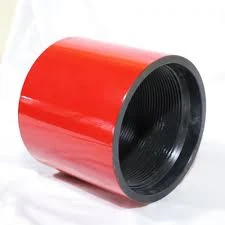
Bull Plugs Functionality and Applications
Bull plugs are integral tools in the oil and gas sector, primarily used as end terminations for piping systems. Often employed during well completion, they are crucial for temporarily sealing sections of piping, ensuring that no debris or unwanted materials enter the wellbore.
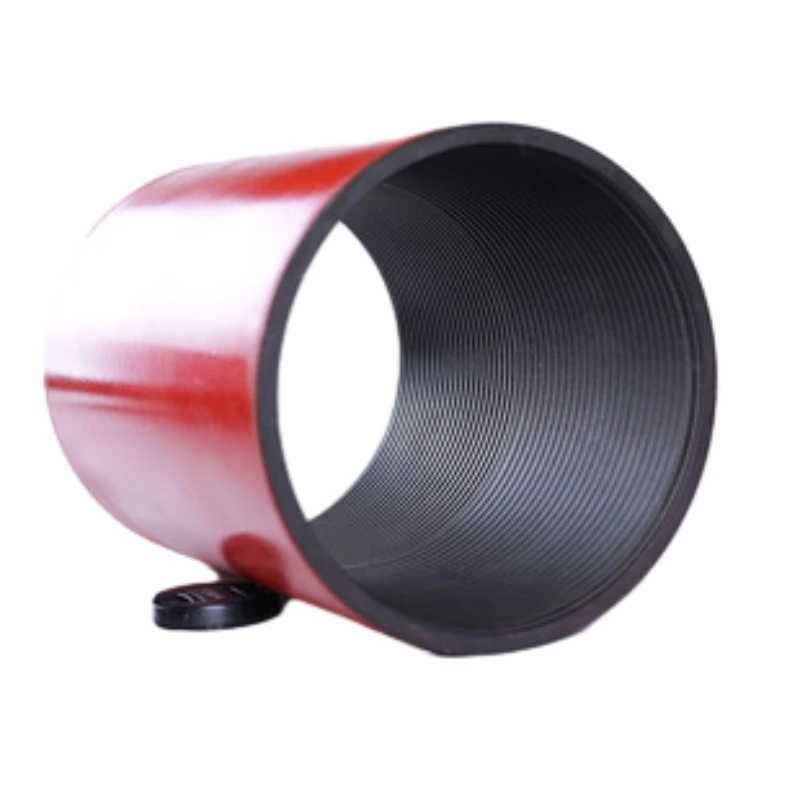
Key features of bull plugs include their robust construction, designed to withstand harsh environmental conditions and high pressure scenarios typical to oil wells. Made from high-grade steel, these plugs are machined with precision to provide a tight seal, preventing leakage and ensuring the integrity of the piping system.
In practical applications, bull plugs are often used in capping off unused sections of a well or pipeline. This capability is vital in dynamic drilling environments where sections of the operation may be temporarily suspended. By providing a reliable seal,
bull plugs allow for safe and controlled operations.
Round Head Plugs Design and Distinction
Round head plugs, on the other hand, are noted for their versatility and adaptability in various drilling and completion tasks. Characterized by their rounded heads, these plugs are typically used for sealing holes or ports that require easy access for future maintenance or modifications.
Unlike bull plugs, round head plugs are designed for situations where frequent access to the sealed section is anticipated. Their design facilitates ease of installation and removal, a feature that significantly reduces downtime during maintenance procedures.
Manufactured from durable materials, round head plugs ensure long-term performance even under challenging conditions. They can be tailored to meet specific project requirements, which makes them an invaluable component in both standard and bespoke well designs.
Comparative Analysis Bull Plug vs Round Head Plug
bull plug vs round head plug
While bull plugs and round head plugs may seem similar at first glance, their applications and specifications highlight distinct differences. Bull plugs are more suited for permanent or semi-permanent sealing, where maximum strength and resistance are required. This makes them ideal for high-pressure scenarios and environments where the plug must remain undisturbed for extended periods.
Round head plugs, however, offer flexibility in applications where accessibility is key. Their design is less about enduring extreme conditions and more about providing a practical solution for openings that need periodic access. As such, round head plugs are frequently found in scenarios where rapid intervention might be necessary.
From an operational standpoint, the choice between a bull plug and a round head plug often boils down to the specifics of the project at hand. Engineers must weigh factors such as required seal integrity, environmental conditions, and maintenance schedules. Understanding these nuances ensures that the right plug is chosen for the task, optimizing both performance and cost-effectiveness.
Real-World Experience and Expert Insights
Drawing from decades of industry experience, operators have noted the importance of selecting the appropriate plug type in minimizing operational disruptions. For instance, in deepwater drilling, where equipment faces immense hydrostatic pressure, using a bull plug could mean the difference between a successful operation and a catastrophic failure.
Conversely, in rigs where routine adjustments and inspections are frequent, round head plugs have proven invaluable. Their ease of use significantly decreases the time technicians spend in potentially hazardous environments, thereby enhancing overall safety.
The expertise of seasoned engineers plays a pivotal role in plug selection and application. With a nuanced understanding of the industry's demands, these professionals guide decisions that uphold safety and efficiency. By fostering an environment of continuous learning and adaptation, the industry ensures that innovations in plug design meet the evolving needs of modern drilling operations.
Conclusion
Selecting between a bull plug and a round head plug is not merely a matter of preference but a critical decision affecting the efficiency and safety of well operations. Their distinct functionalities cater to different needs within oil and gas projects, making it essential for operators to carefully consider their choice based on specific operational requirements.
With the continuous advancement in material science and engineering, the future holds promise for even more refined plug solutions, enhancing both performance and reliability. As the industry marches towards greater technological integration and precision, the role of bull plugs and round head plugs will undoubtedly remain central to drilling success.