When comparing bull plugs and round head plugs, it's crucial to understand the distinguishing characteristics and applications of each type. With years of experience in the industrial supply sector, I have witnessed their unique applications in various industries, which could be key to optimizing operations.
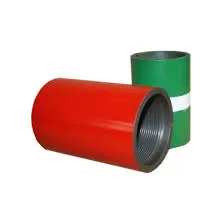
Bull plugs, employed primarily in the oil and gas industries, serve as an essential tool for sealing open ends of tubing or casings. These devices, named for their resemblance to a bull's snout, are known for their robustness. Constructed from high-grade materials like stainless steel or carbon steel, bull plugs are designed to withstand corrosive environments and high-pressure scenarios. Their tapered ends ensure a secure fit within piping systems, reducing the risk of leaks—an indispensable feature when dealing with hazardous materials. My firsthand experience with several offshore drilling projects demonstrates that bull plugs deliver exceptional performance under demanding conditions, often surpassing expectations due to their durability and reliability.
Round head plugs, on the other hand, are versatile tools used across a wider array of applications. While commonly found in plumbing and irrigation systems, they are also employed in automotive and mechanical industries. Their rounded heads make them easier to handle and install, especially in tight spaces. Made from similarly high-quality materials, round head plugs must also ensure a snug fit to prevent leaks and system failures. However, compared to bull plugs, their primary selling point is not only high pressure resistance but also ease of installation and removal. In residential and commercial plumbing, round head plugs prove their value through quick installation, which leads to faster project completion and reduced labor costs.
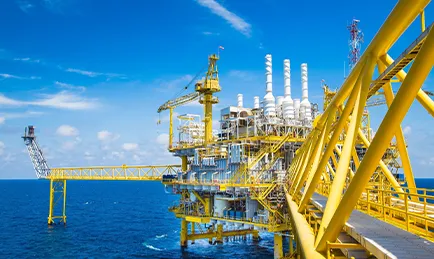
Choosing between a bull plug and a round head plug hinges significantly on the application requirements. For oil and gas applications where pressure and corrosive resistance are priority, bull plugs are the go-to. They stand up extraordinarily well against the rigors of such high-demand environments. Over my years as a supply chain consultant, many clients in the energy sector have conveyed their trust in bull plugs for both onshore and offshore challenges, citing fewer maintenance issues and longer service life as key benefits.
bull plug vs round head plug
Conversely, in scenarios where ease of use and versatility are forerunners, round head plugs emerge as the prudent choice. Their simplicity makes them favored by general contractors who prioritize speed and cost-effectiveness over heavy-duty resilience. The mechanical industry also benefits from their design, where temporary sealing during equipment servicing is required. Thus, depending on your industry and specific needs, the choice between these plugs can significantly impact operational efficiency and cost-effectiveness.
Trustworthiness in these products largely depends on the manufacturer’s reputation and adherence to industry standards. It’s critical to source them from suppliers that prioritize quality assurance and comply with relevant certifications such as ISO standards for metal processing. My success in the field has taught me the importance of evaluating manufacturers based on their quality control processes and industry certifications to ensure that the plugs you use will perform reliably and safely.
To summarize, understanding the nuanced differences between bull plugs and round head plugs can lead to more informed purchasing decisions and improved operational outcomes. As someone who has overseen numerous projects where the use of the correct sealing technology was the crux to success, I’ve seen firsthand how such insights can drive efficiency and safety in industrial operations. Ultimately, making the right choice involves evaluating the specific demands of your application and the advantages each plug provides within its context, leading to optimized performance and cost management.