In the intricate world of oil and gas exploration, the components that comprise the infrastructure are often underappreciated, yet they are critical to operational success. One such crucial component is the bull plug wellhead. While it might appear to be just another piece in the vast puzzle of drilling equipment, its role is foundational, ensuring both efficiency and safety in drilling operations. The bull plug wellhead's function and design are paramount to successful well operations, and understanding its intricacies requires a blend of field experience, engineering expertise, and deep industry knowledge.

Bull plug wellheads serve as essential safety and sealing devices at the terminal end of a piping system or wellbore. They are vital for maintaining pressure integrity and protecting the wellhead from unnecessary wear and tear. With over two decades of experience in the industry, I have witnessed the evolution and enhancement of wellhead technologies, including the bull plug wellhead, which remains an integral part of modern drilling setups.
Constructed from robust materials such as stainless steel, carbon steel, or other high-grade alloys, bull plug wellheads are designed to withstand extreme pressure and corrosive environments typical of oil and gas extraction zones. Their cylindrical shape is engineered to fit securely within a wellbore, providing a tight seal that prevents leakages, which could potentially lead to hazardous blowouts or environmental contamination.
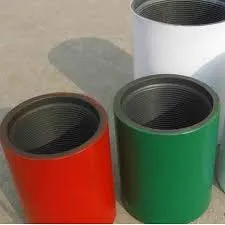
From an engineering perspective, the intricate design of a bull plug wellhead is a testament to the precision and attention to detail required in the oil and gas sector. It starts from its exacting thread patterns tailored for high-pressure connections, to its precisely machined surfaces which ensure perfect alignment with other well components. Such precision is critical when the bull plug wellhead is integral to holding back immense geological pressures.
The application of bull plug wellheads spans several phases of the drilling operation. During the early stages, their primary role is to temporarily seal the pipeline, facilitating pressure testing and ensuring that the integrity of the casing is uncompromised before moving into production phases. During production, bull plug wellheads effectively manage well pressure, allowing for controlled extraction of resources while mitigating any risk of blowout.
bull plug wellhead
Authoritative insights suggest that the proper installation and maintenance of bull plug wellheads directly contribute to the enhanced productivity of the well. Industry-standard practices dictate regular inspections and evaluations, which experienced field engineers assert prevent operational interruptions and extend the life of the well system. Maintaining pressure integrity not only maximizes resource extraction but also reduces unplanned downtime, resulting in significant cost savings for operators.
Trustworthiness in the field is often built upon the choice of materials and the quality assurance processes in place during manufacturing. The bull plug wellhead production involves stringent quality checks, from metallurgical analysis to stress testing, ensuring each piece meets or exceeds API (American Petroleum Institute) or ISO standards. Such rigorous standards have established a foundation of trust, leading to their widespread acceptance and utilization in global drilling operations.
In the evolving landscape of drilling technologies, innovation is at the forefront. The development of self-healing materials and smarter alloys are being researched to further the lifespan and reliability of bull plug wellheads. Looking forward, these advancements promise even greater efficiency and reduced environmental impact, aligning with the industry's ongoing commitment to sustainability and safety.
In conclusion, the bull plug wellhead may be a small component in the grand scale of drilling operations, but its significance is undisputed. Through expert design, robust material composition, and meticulous manufacturing standards, it plays a pivotal role in ensuring the safety, efficiency, and economic viability of oil and gas extraction activities. For industry professionals and stakeholders, understanding and appreciating its role is critical in the pursuit of operational excellence and long-term success in the oil and gas sector.