Ensuring Integrity in Casing and Tubing Connections
In the realm of oil and gas exploration and production, the integrity of casing and tubing connections is paramount. These connections serve as the backbone of well construction, ensuring that the high-pressure environments deep within the earth do not compromise the structural stability of the wellbore. The importance of their reliability cannot be overstated, as failure can lead to catastrophic consequences, including environmental pollution and financial loss.
Casing is the steel pipe that lines the borehole, providing a conduit for the extraction of hydrocarbons while preventing the influx of fluids from the surrounding geological formations. Tubing, on the other hand, is a smaller diameter pipe placed inside the casing to transport the extracted fluids to the surface. The connection between these pipes must withstand not only the immense weight of the earth above but also the aggressive chemical properties of the extracted substances.
The design of casing and tubing connections has evolved over time to meet these rigorous demands. Early designs featured simple threaded connections, which, while effective, were prone to leakage and damage under stress. Advancements led to the development of more sophisticated connection types such as threads sealed with elastomers or metal-to-metal seals, offering improved resistance to both mechanical load and corrosive materials.
Modern casing and tubing connections employ a variety of technologies to enhance their performance. For example, torque-turn technology ensures that each connection is made up with consistent pressure, reducing the risk of under- or over-tightening. Additionally, advanced materials science has enabled the creation of specialty alloys that can resist the extreme conditions found in deep wells Additionally, advanced materials science has enabled the creation of specialty alloys that can resist the extreme conditions found in deep wells
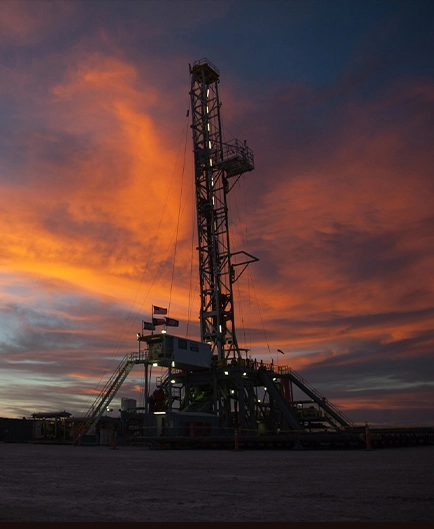
Additionally, advanced materials science has enabled the creation of specialty alloys that can resist the extreme conditions found in deep wells Additionally, advanced materials science has enabled the creation of specialty alloys that can resist the extreme conditions found in deep wells
casing and tubing connections.
Despite these advancements, the installation process remains critical. Field personnel must adhere to precise procedures during the make-up of connections to prevent errors that could weaken the joint. This includes proper cleaning, application of thread compound, and correct torquing techniques. Quality control measures such as pressure testing and radiographic inspection are often employed to verify the soundness of connections before the casing or tubing is run into the well.
Furthermore, ongoing research aims to improve the non-destructive testing methods used to evaluate connections. Sophisticated ultrasonic and magnetic flux leakage testing can detect minute flaws that might escape the naked eye, adding another layer of confidence in the well's structural integrity.
In conclusion, casing and tubing connections are essential components in the quest for efficient and safe hydrocarbon extraction. As technology continues to advance, so too will the methods by which we ensure these connections remain secure and reliable. The future holds promise for even more resilient designs, contributing to an industry that strives for excellence in both operational success and environmental stewardship.