Casing and tubing connections play an integral role in the petroleum and natural gas industries, acting as the backbone of efficient and safe extraction processes. These connections are critical for maintaining the integrity of wells, ensuring seamless operations, and minimizing environmental impact. Making informed choices about casing and tubing connections can significantly influence the overall success and longevity of drilling projects.
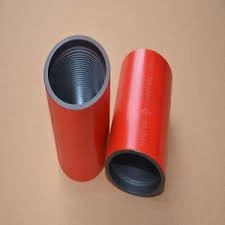
Understanding the distinction between casing and tubing is essential for optimizing their use. Casing refers to the large diameter pipe lowered into a well and cemented in place to protect the surrounding soil or rock. Tubing, on the other hand, is the smaller diameter pipe that runs inside the casing, facilitating the direct transport of oil and gas to the surface. Each has its unique connection requirements and specifications, demanding precise engineering solutions.
The engineering behind these connections is highly specialized. It involves selecting materials that can withstand extreme pressure and temperature conditions while preventing leakages. A deep dive into metallurgy reveals that high-strength steel grades are often employed for both casing and tubing to cope with the elevated stresses encountered during drilling and production. Moreover, advanced coatings are sometimes applied to combat corrosion—one of the enduring challenges in downhole environments.

In terms of connection designs, the market offers a variety of options. Threaded and coupled connections are common, favoring operations where rapid assembly and disassembly are required. However, premium connections, characterized by gas-tight seals and robust structural integrity, are increasingly favored in high-stakes scenarios such as deep-sea drilling or formations with high concentrations of corrosive elements like hydrogen sulfide.
Field experience reiterates the importance of connection reliability. Reports from drilling sites highlight that improperly fitted connections can lead to catastrophic failures, resulting in costly downtime and potential spills. Experienced operators emphasize the need for regular inspection and testing protocols, utilizing techniques such as ultrasonic testing or pressure testing to verify connection integrity before deployment.
casing and tubing connections
An emphasis on expertise is necessary in both selecting and implementing casing and tubing connections. Drilling engineers, along with metallurgists and geotechnical experts, collaborate to tailor connection types to specific project requirements. This multidisciplinary approach considers factors such as the geological formation, well depth, expected pressure differentials, and anticipated production volume. Custom solutions are often sought after for unconventional wells, where traditional connections may not offer reliable performance.
Trustworthiness in casing and tubing connections is compounded by adherence to stringent industry standards. The American Petroleum Institute (API) and the International Organization for Standardization (ISO) set forth guidelines that ensure the fitness of connections for varied oilfield applications. These standards are not merely checkboxes but crucial safety nets that safeguard the environment and operational personnel.
On the practical side, maintaining authoritative knowledge about the latest advancements in connection technology can grant companies a competitive edge. Innovations in connection designs—incorporating automation, digital monitoring, and enhanced materials—promise to revolutionize the efficiency and safety of drilling operations. By investing in research and development, companies are actively pushing the frontier of what's possible, introducing smart connections that automatically adjust to environmental conditions in real-time.
In conclusion, the complex interplay of experience, expertise, authoritativeness, and trustworthiness underscores the critical nature of casing and tubing connections in the energy sector. Companies that successfully harness these elements position themselves to not only achieve operational excellence but also uphold the highest standards of safety and environmental stewardship. In an industry where precision is paramount, the integrity of these connections ultimately determines the stability and productivity of oil and gas extraction efforts.