Casing and tubing connections are integral components in the oil and gas industry, serving as the backbone for efficient and safe transportation of hydrocarbons from the reservoir to the surface. As a critical aspect of well integrity, these connections demand a high degree of precision and reliability to withstand extreme conditions, such as high pressure and corrosive environments.
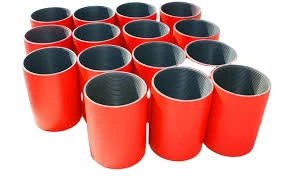
In the realm of product expertise, understanding the nuances of casing and tubing connections involves appreciating the engineering feats behind these threaded and coupled joints. These components are designed to handle considerable tensile loads and prevent leakage, which could otherwise lead to catastrophic failures. The connections are typically made from high-grade steel alloys and undergo rigorous testing to ensure they meet stringent standards set by bodies such as the American Petroleum Institute (API).
Real-world experience underscores the importance of selecting the right type of connection for specific geological and operational conditions. With several types of connections available, such as Buttress threads, Extreme-Line threads, and Premium connections, each offers distinct advantages. For instance, Buttress threads are commonly used in shallow wells due to their robustness and ease of maintenance. Meanwhile, Premium connections are favored in deeper or more deviated wells where gas-tight seals are crucial.

Authoritativeness in casing and tubing connections is often demonstrated by manufacturers with a proven track record and certifications. Established companies like Tenaris, Vallourec, and TMK not only produce high-quality products but also invest in research and development to innovate connection technologies. For instance, advancements in seal integrity and fatigue resistance have significantly enhanced the performance of these connections in challenging offshore environments.
casing and tubing connections
Trustworthiness is built through adherence to international standards and consistent performance over time. The reliability of casing and tubing connections is not just a matter of engineering but also involves comprehensive quality control processes. From material selection and heat treatment to non-destructive testing, each step ensures that the connections can withstand the operational life of the well.
From a product standpoint, understanding the lifecycle of casing and tubing connections involves considering factors such as installation, maintenance, and replacement.
Installation is a critical phase where precise torque and angle measurements ensure the structural integrity of the connection. Regular maintenance practices, including periodic inspections and pressure tests, help identify potential issues before they escalate into major problems. Eventually, the end-of-life replacement decision is guided by factors such as wear and tear, evolving operational demands, and technological advancements.
In conclusion, the effective utilization of casing and tubing connections hinges on a synergy of expertise and experience, backed by manufacturers' authority and the products' inherent trustworthiness. By emphasizing these facets, stakeholders can ensure optimal operation and longevity of oil and gas wells, thereby safeguarding their investments and enhancing overall operational efficiency.