Precision in oil and gas operations hinges significantly on the choice of casing and tubing connections, a topic resonating with profound expertise and long-standing industry experience. The meticulous selection of these components directly influences the operational efficiency and safety of exploration and extraction processes, necessitating a thorough understanding of their nuances.
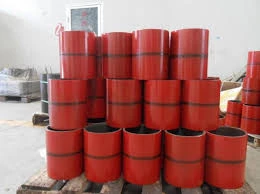
Casing and tubing connections, pivotal in the seamless integration of oilfield tubular goods, are not merely joints that link pipes; they are the linchpin securing the integrity of well operations. Each connection serves as a critical seal, withstands dynamic loads, and resists corrosive environments, making their role indispensable in ensuring seamless extraction.
Delving into the technical aspects, premium connections are tailored meticulously to withstand the pressures and temperatures well exceeding typical operational thresholds. Expertise in this field underscores the development of connections featuring advanced thread geometries and enhanced material compositions. This sophisticated engineering approach curtails the risk of connection failure, thereby safeguarding investments in high-stakes exploration projects.
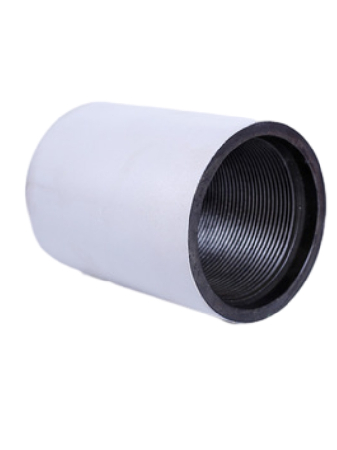
Decades of field experience accentuate the importance of variable geometry in connection design. Thread profiles, tailored to specific well requirements, present an optimized contact area that reduces stress concentrations—a critical factor under cyclic loading conditions. This precision engineering facilitates enduring performance under varying thermal and mechanical stresses, thus prolonging the lifespan of the well.
Reflective of an authoritative stance, leading manufacturers deploy rigorous testing regimens to validate connection performance under simulated well conditions. This authoritative process encompasses testing for tensile strength, compression tightness, and resistance to wear and tear, all designed to simulate the harshest drilling environments.
Such stringent standards elevate the credibility of premium connections in high-pressure, high-temperature wells.
casing and tubing connections
Moreover, trust in casing and tubing connections is bolstered through stringent global standards and certifications. The adherence to ISO and API standards guarantees that connections meet a universal benchmark of quality, engendering a shared confidence among stakeholders in their performance capabilities. Manufacturers often participate in third-party audits to align with these standards, ensuring transparency and accountability in connection quality.
Addressing the real-world application of this knowledge, field engineers consistently report improved well outcomes following the adoption of precision-engineered connections. Anecdotal evidence from seasoned practitioners points to reduced downtime and maintenance costs, attributed to these connections' high resilience and adaptability. These experiences resonate across major oil fields, underscoring the tangible benefits of opting for quality connections in challenging scenarios.
In the digital age, sharing of expertise through platforms and forums allows for a continuous exchange of insights regarding casing and tubing innovations. The collaborative learning environment facilitates the advancement of connection technologies, with industry veterans imparting valuable wisdom to emerging engineers.
In conclusion, the intricate balance of experience, expertise, authority, and trustworthiness defines the narrative of casing and tubing connections in the oil and gas sector. Each element—proving indispensable—contributes to the overarching goal of optimizing well integrity and performance. Investing in high-quality connections not only mitigates operational risks but also aligns with the industry's demand for safety, efficiency, and environmental stewardship. As technology evolves, so too will the standards of these critical components, paving the way for more innovative solutions in the realm of subsurface resource management.