Casing collars play a critical role in the drilling and completion phases of well construction. These essential components are meticulously designed to ensure the integrity and efficiency of oil and gas extraction processes. By providing a robust connection point for casing sections, casing collars help maintain the structural stability of wells, preventing potentially costly failures and environmental hazards. Delving into the intricacies of casing collars unveils the unmatched experience and expertise required to design and implement this crucial tool within the oil and gas industry.
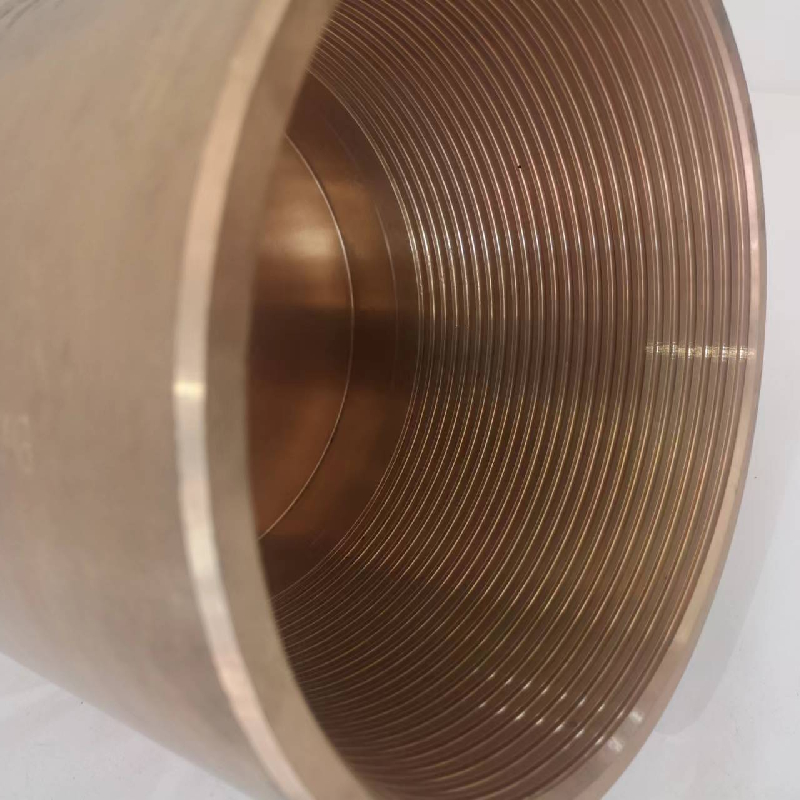
With decades of innovation and technological advancement behind them, today’s casing collars embody the pinnacle of engineering prowess in the field. These collars are often crafted from high-quality, alloyed steel that ensures durability, resistance to extreme pressures, and corrosion resistance. Moreover, the precision with which these collars are manufactured is paramount to their effectiveness. Tolerances are incredibly tight, often within microns, which necessitates a deep understanding of metallurgical properties and machining techniques.
The expertise in producing casing collars lies not only in the understanding of materials and engineering principles but also in the precise execution needed to meet application-specific requirements. Manufacturers employ advanced techniques such as CNC machining and inspection technologies that have set new industry standards for precision. Continuous professional development and investments in cutting-edge technology equip manufacturers with the knowledge to manage the complexities of wellbore architecture, thus ensuring collars meet the required specifications for different well environments, from conventional vertical wells to complex horizontal or offshore wells.

casing collar
Authoritativeness stems from a manufacturer’s ability to consistently deliver products that perform superbly under challenging conditions. Companies leading the market in casing collars often participate actively in industry standards committees, such as the American Petroleum Institute (API). By adhering to the stringent standards set forth by these authoritative bodies, manufacturers demonstrate a commitment to quality and safety, bolstering their reputation and credibility within the industry. Their collaboration with research institutions and participation in symposiums further positions them as frontrunners who shape the future of drilling technology.
Trustworthiness, in the realm of casing collars, is largely reliant on consistent performance, transparent practices, and a commitment to sustainability. Trust is built when manufacturers openly test and verify the performance of their products in various simulated environments, providing customers with data that can be relied upon when making purchase decisions. Moreover, ethical sourcing of raw materials and adherence to environmental regulations are key trust indicators that discerning clients consider. In an industry where the smallest misstep in equipment integrity could lead to catastrophic results, having trust in the quality and accountability of casing collar suppliers is non-negotiable.
The combined elements of experience, expertise, authoritativeness, and trustworthiness ensure that casing collars are not merely a product but a cornerstone of successful well completion and operation. The ongoing evolution in their design and application reinforces their role as a linchpin in the energy sector, providing the backbone for safe and efficient energy production. As the quest for more sustainable and efficient energy solutions continues, so does the imperative for casing collars to evolve, maintaining their pivotal role in the progression of the oil and gas industry.