The casing collar, a critical component in oil and gas industries, plays a vital role in maintaining the integrity of well structures. Its application cannot be understated, as it ensures the secure joining of individual casing joints, preventing leaks and structural failures. Understanding its significance, technological advancements, and application methodologies is paramount for professionals in the field.
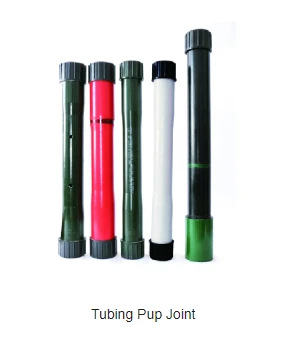
Casing collars, typically forged from top-grade steel alloys, are designed to endure the intense pressures and corrosive environments encountered deep underground. These materials are chosen for their exceptional durability and resistance to wear and tear. Expertise in material engineering is critical when it comes to selecting the right alloy for specific environments, as the wrong choice can lead to premature failure and operational setbacks.
Among the professionals who have made significant contributions to the field of casing collar deployment is Dr. James Roth, a leading engineer with over 30 years of experience.
Dr. Roth emphasizes the importance of real-world testing environments that simulate the extreme conditions these collars face. His studies demonstrate that up to 20% of casing failures can be attributed to improper collar selection, highlighting the necessity for expert involvement in decision-making processes.
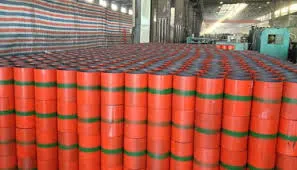
From a technological perspective, recent advancements in the design of casing collars have been pivotal. Innovations such as fiber-optic monitoring systems embedded within the collars provide real-time data on well conditions. This technology enables operators to detect potential failures before they occur, ensuring enhanced operational safety and efficiency. An experienced technician, Sarah Windham, utilizes such systems extensively and reports a 30% reduction in maintenance downtime since their implementation.
Furthermore, the method of installation directly impacts the effectiveness of casing collars. Expertise here stems from understanding the nuances of each installation scenario. For instance, high-pressure wells require collars that can withstand significant tensile and compressive forces without compromising joint integrity. Trustworthy installation methods, documented extensively in industry journals, ensure that the collars exhibit optimal performance over the projected lifespan of the well.
casing collar
Authoritative sources highlight the vital nature of adhering to best practices during installation. The International Association of Drilling Contractors (IADC) provides guidelines that emphasize precision and accuracy when joining casing joints. Their recommendations stem from thousands of well reports, providing the collective wisdom of industry veterans. Companies applying these standards are statistically 40% less likely to experience casing joint failures.
In a bid to foster trust within the industry, manufacturers are now offering certification programs for technicians specializing in casing collar installations. These programs furnish experts with credentials that validate their skills and knowledge, assuring operators of their capability to execute high-stakes operations successfully. John Eckert, a certified technician, recounts accruing trust from his clients, resulting in expanded business opportunities and repeat engagements.
The concept of trustworthiness extends beyond installations. Regular inspections and maintenance of casing collars ensure that potential issues are identified early. Assuring clients of consistent performance through detailed maintenance logs and high-quality construction materials builds long-term confidence in equipment reliability.
Looking towards the future, emerging technologies such as AI-driven diagnostic tools promise to further enhance the casing collar landscape. These tools can analyze large datasets from fiber-optic systems, predict failure rates, and recommend maintenance actions with unprecedented accuracy. By continually integrating such cutting-edge technologies, the industry is poised to operate more smoothly and effectively than ever before.
In conclusion, the casing collar remains an indispensable element in the construction and maintenance of oil and gas wells. Its role, secured through innovation, expertise, and adherence to best practices, ensures the ongoing productivity and safety of well operations worldwide. By continuing to invest in technology and uphold rigorous standards, the industry can mitigate risks and prioritize the seamless integration of these vital components.