Casing collars are pivotal components in the oil and gas industry, providing critical connections in wellbore casing strings. They are fundamental in ensuring the integrity and stability of the well, which is vital in both drilling and production phases. This article delves into the importance, function, and selection criteria of casing collars based on years of expertise in the field.
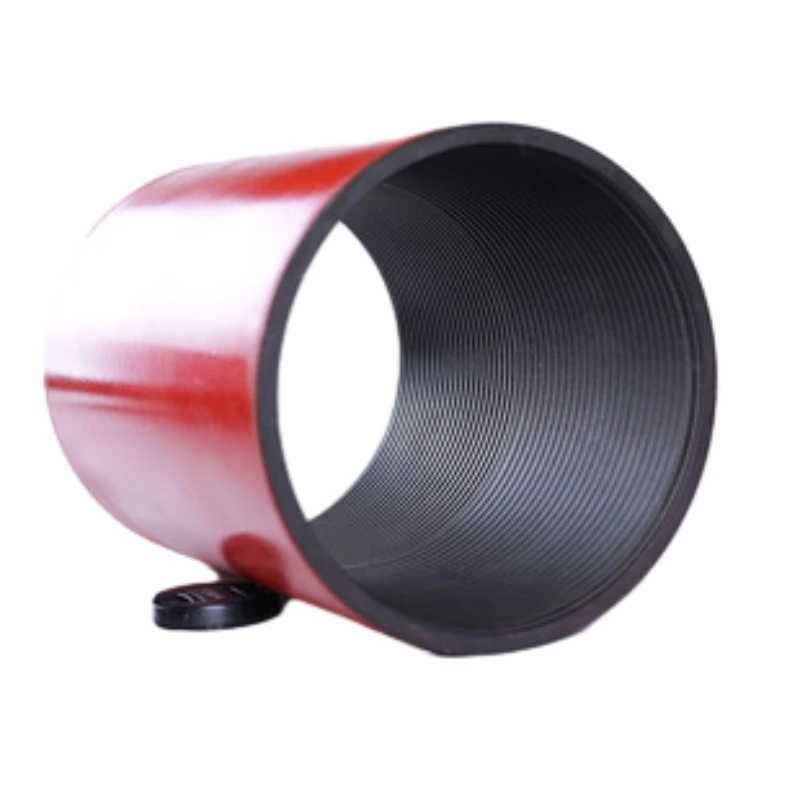
In the exploration and production of oil and gas, maintaining the structural integrity of a well is paramount. Casing collars, cylindrical sections usually made from high-grade steel, serve as joining elements in the series of pipes known as casing strings. These collars form watertight and pressure-tight seals at the joints, preventing oil, gas, and drilling fluids from seeping into surrounding earth formations.
Experience in well operations confirms that the correct installation and functioning of casing collars can prevent costly failures. A well-engineered casing collar ensures seamless transmission of loads and stresses across casing strings, which can be particularly challenging in horizontal and high-pressure high-temperature (HPHT) wells. By ensuring structural stability, these components mitigate risks of blowouts and minimize operational downtime, enhancing both safety and profitability.
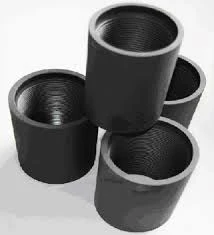
From an expertise standpoint, casing collars are designed to meet specific environmental and operational demands. Selecting the appropriate casing collar involves a thorough understanding of the well conditions and requirements. For example, the material must be capable of withstanding corrosive substances, variable temperatures, and immense pressures. Advanced alloys and protective coatings are often employed to enhance durability and extend the service life of these components.
Casing collar threads present another critical aspect of their engineering. The thread design—often meticulously tested and verified—is crucial for ensuring secure joint connections. Premium thread types, such as Buttress and VAM, are commonly chosen for their enhanced load-carrying capacity and resistance to fatigue. When engineers select these threads, they rely on data-driven methodologies and rigorous testing to verify performance under simulated well conditions.
casing collar
Authoritativeness in the field is underscored by adherence to industry standards. Leading manufacturers and engineers work in compliance with globally recognized standards such as those set by the American Petroleum Institute (API). These standards ensure uniformity, safety, and reliability in casing collar production and application, reassuring operators of their quality and performance.
Trustworthiness in a manufacturer or supplier of casing collars is established through transparent practices and a strong reputation for quality assurance. It is critical to partner with companies that provide comprehensive documentation, including material certificates, manufacturing traceability, and performance testing results. This transparency instills confidence in operators that the products will perform as expected in the challenging operational environment.
In addition, deploying digital technologies for enhanced well monitoring and data analytics further strengthens trust in casing collar applications. Real-time data acquisition and analysis enable operators to detect anomalies and address potential issues before they develop into major problems.
In conclusion, casing collars are indispensable to the successful completion and operation of oil and gas wells. Their design, material selection, and thread engineering must cater to the specific demands posed by the operational environment. Collaborating with authoritative manufacturers who uphold stringent quality standards and leverage cutting-edge technology ensures the reliability and effectiveness of these critical components. Such strategies reinforce operational efficiency and safeguard investments in a volatile industry.