Choosing the right casing coupling is pivotal for the successful drilling and completion of oil and gas wells. These critical components ensure a secure connection between casing pipes, thereby playing an indispensable role in maintaining well integrity and preventing potential leakages. The journey of selecting an appropriate casing coupling involves a blend of technical knowledge, expert recommendations, and field-proven experience.
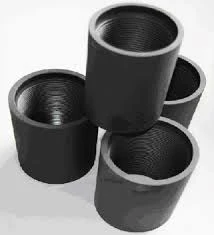
Casing couplings are primarily categorized into two types API (American Petroleum Institute) standard couplings and premium couplings. API standard couplings are widely recognized for their adherence to set specifications, including material grade, tensile strength, and connection types.
They are a cost-effective solution for wells with basic operational requirements. On the other hand, premium couplings are engineered to tackle more demanding environments, such as high-pressure, high-temperature (HPHT) wells. These couplings are designed to offer enhanced sealing capabilities and reduced risk of galling, thus ensuring higher reliability under extreme conditions.
The material of the casing coupling is a critical factor. While carbon steel is commonly used due to its strength and cost-effectiveness, advanced materials like CRA (corrosion-resistant alloys) are preferred in corrosive environments. CRA materials significantly extend the lifespan of the coupling by resisting the detrimental effects of corrosive gases like CO2 and H2S. Consequently, investment in high-quality materials can lead to cost savings in the long run through reduced maintenance and downtime.
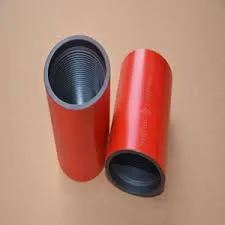
Technological advancements in the manufacturing of casing couplings have greatly influenced their performance. The introduction of computer numerical control (CNC) machines has enhanced the precision in manufacturing, leading to better dimension control and thread compatibility. This precision minimizes the likelihood of failure in the field, thereby improving overall operational efficiency. Furthermore, innovations such as friction welding and spin forming have contributed to superior coupling performance by ensuring uniform material properties and better structural integrity.
casing coupling
From a professional perspective, one cannot overlook the importance of certification and field-testing. Ensuring that the casing coupling complies with industry standards and has been rigorously field-tested under simulated conditions adds to the product's credibility. This not only underscores its reliability but also reassures oil and gas operators of its performance under actual operating conditions.
Collaboration with reputable suppliers and manufacturers who possess a robust track record is crucial. Expert advice and field support from these partners can greatly alleviate the challenges faced during the selection process. Suppliers with a deep understanding of the engineering aspects and real-world applications of casing couplings can offer invaluable insights, ensuring that the chosen products meet the specific demands of any given well environment.
To sum up, the experience and expertise shared by industry veterans heavily emphasize the need for thorough due diligence in the selection of casing couplings. A strategic approach—balancing initial investment with long-term performance—is essential. Opting for high-quality, well-tested products from reputable manufacturers not only enhances operational safety and efficiency but also establishes a strong foundation of trust and reliability in the demanding field of oil and gas extraction.