Casing couplings, the unsung heroes in the oil and gas industry's drilling process, play a pivotal role in ensuring the integrity of wellbore operations. These small yet mighty components are designed to connect lengths of casing pipes and provide a reliable seal that prevents leakage of drilling fluids and hydrocarbons, thereby safeguarding both the environment and the efficiency of drilling operations. Understanding the nuances of casing couplings is essential for anyone involved in the extraction of oil and gas.
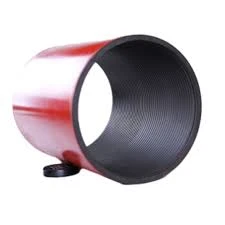
A comprehensive understanding of casing couplings begins with recognizing their function within the broader system of casing. Casing is a series of steel pipes that are cemented in place to stabilize the well, prevent contamination of water formations, and maintain the integrity of the wellbore. Casing couplings are threaded connectors that join each segment of the casing, creating a continuous protective lining from the surface to the oil and gas formation. The precision involved in their design cannot be overstated; a failure at this juncture could lead to catastrophic ruptures, significant financial loss, and environmental disaster.
The strength and durability of casing couplings hinge on several factors, including material composition, threading type, and manufacturing standards. Most couplings are made from varieties of carbon steel, known for their ability to withstand the immense pressures and harsh conditions present in deep drilling operations. Advanced chemical treatments enhance their resistance to corrosion and high temperatures, extending their lifespan and reliability.
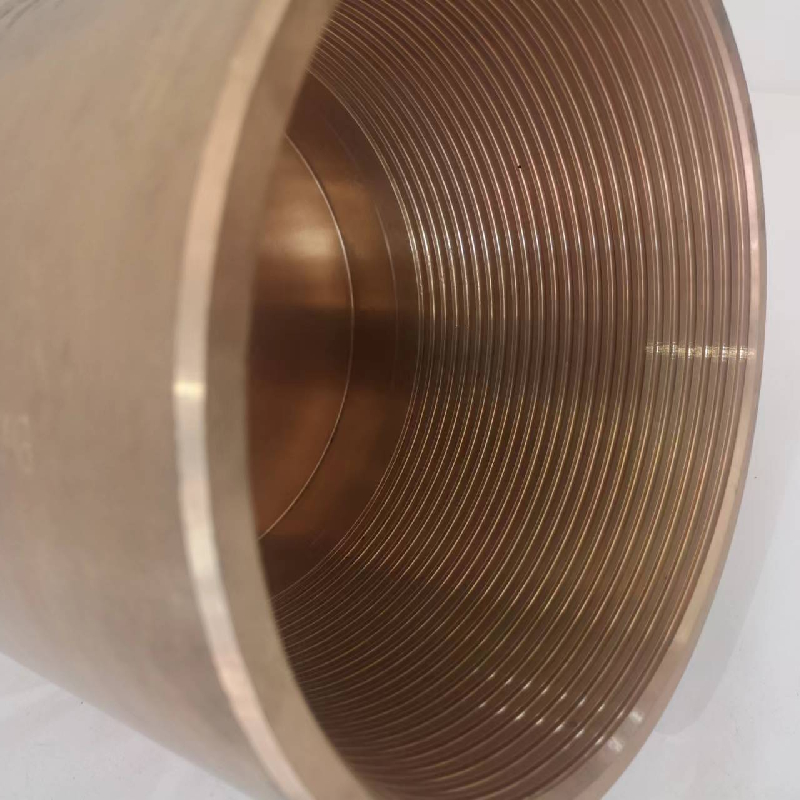
Threading is a critical aspect that warrants attention, as it determines the ability of the coupling to maintain a tight seal under fluctuating pressures. Industry standards like those set by the American Petroleum Institute (API) —specifically API 5CT— provide guidelines for threading configurations that ensure compatibility and performance. For professionals seeking enhanced performance, premium threading options offer tighter seals, greater strength, and better resistance to wear and tear.
From an engineering perspective, the manufacturing process of casing couplings involves rigorous quality control to ensure compliance with industry standards. High-precision CNC machines are employed to cut threads with exacting accuracy. Each coupling undergoes extensive testing, from pressure tests to metallurgical analysis, to certify its efficacy and safety.
casing coupling
Field professionals and procurement managers prioritize couplings from reputable manufacturers who demonstrate a commitment to quality and innovation. Vendors with a proven track record of reliability and adherence to regulatory standards cultivate trust. Testimonials and case studies often highlight the difference made by high-quality couplings in successful drilling operations, enhancing their perceived expertise and authoritativeness.
The topic of casing coupling quality doesn't just end with the initial purchase. Proper handling and maintenance extend their usability. Protections during shipping and careful handling during installation prevent thread damage and ensure optimal performance. Additionally, regular inspections and adherence to installation protocols mitigate risks and extend the functional life of the couplings.
Selecting the right casing coupling involves consideration of the geological conditions of the target drilling site. Engineers must weigh factors such as the formation's pressure, temperature, and chemical composition to choose couplings that can withstand these unique challenges. Custom solutions cater to extreme environments, such as high-pressure, high-temperature (HPHT) wells, where standard options might fall short.
Moreover, emerging technologies in material science and engineering are paving the way for smarter designs and better materials. Composite materials and corrosion-resistant alloys are gaining traction in the quest for longer-lasting and more resilient solutions. These innovations not only drive efficiency but also reduce costs and environmental hazards, aligning the industry with modern demands for sustainable and responsible energy extraction.
Casing couplings, therefore, are much more than mere connectors. They are crucial components of a larger assembly that preserves the safety, financial viability, and environmental integrity of oil and gas extraction efforts. Their design, material selection, and ongoing maintenance are all important considerations for a successful drilling operation. Understanding this multifaceted product marks true expertise in the field, guiding those involved toward selections that prove beneficial in the short and long term. High-quality casing couplings serve as a testament to the industry's commitment to safety, reliability, and innovation.