Casing couplings play a critical role in the oil and gas industry, ensuring the seamless joining of casing pipes that form the backbone of any drilling operation. Understanding the dimensions of these couplings is essential for optimizing performance, ensuring safety, and enhancing the longevity of oil wells.
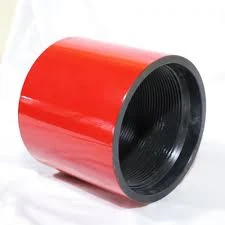
In the context of oil well construction, casing couplings serve as vital connectors that join sections of casing pipes together. These couplings are crafted to handle extreme conditions prevalent in drilling environments, such as high temperature, pressure, and corrosive substances. An in-depth understanding of casing coupling dimensions can significantly affect the outcomes of drilling operations.
Why dimensions matter The dimensions of casing couplings directly impact the structural integrity, pressure capacities, and corrosion resistance of the entire casing assembly. The outer diameter (OD), inner diameter (ID), and wall thickness are three core dimensions that influence how these couplings will perform under various conditions. A precisely matched OD and ID ensure a snug fit, preventing undesirable movement or leakage that could compromise well integrity.

Precision machining The manufacturing of casing couplings adheres to stringent industry standards set by API (American Petroleum Institute) to ensure a high level of performance and reliability. Each coupling is machined with precision to meet specific design criteria which include not only standard dimensions but also finer tolerances that account for material expansion and contraction under thermal stress.
Material selection The choice of material for casing couplings is heavily influenced by operating conditions. Steel grades such as J55, L80, and P110 are commonly used, each offering varying levels of tensile strength and corrosion resistance to suit specific well environments. It's not just the dimensions that need to match; the mechanical properties of these materials must align perfectly with the demands of the drilling operation to avoid catastrophic failures.
casing coupling dimensions
Dimension customization Despite standardization, customization of coupling dimensions is often required to meet unique well specifications or to integrate new technologies. Custom couplings can be manufactured to accommodate special threads, larger diameters for deeper wells, or enhanced material coatings for increased durability against harsh chemical exposures.
Industry expertise and innovation The expertise involved in designing and manufacturing casing couplings is multidimensional, drawing from fields such as materials science, engineering, and field research. Leading manufacturers are consistently innovating to enhance coupling design, focusing on improving seal integrity and reducing connection time through advanced engineering techniques like automation in manufacturing.
Ensuring reliability Real-world experience has underscored the necessity of regular inspection and maintenance of casing couplings throughout their lifecycle. Employing non-destructive testing methods such as ultrasonic testing can preemptively identify dimensional discrepancies or material defects, thereby averting potential operational disruptions.
Trust in proven solutions Choosing casing couplings from reputable manufacturers who comply with global standards and regulations is paramount. Established suppliers who prioritize quality assurance provide not only components that fit the specified dimensions but also offer comprehensive support services ranging from installation guidance to failure analysis.
In conclusion, the dimensions of casing couplings are integral to the successful implementation and operation of oil wells. Couplings act as the unsung heroes that maintain the integrity and efficiency of drilling operations under some of the most demanding conditions on Earth. Whether opting for standard sizes or bespoke solutions, understanding these dimensions is crucial to aligning operational goals with operational realities, ensuring both the safety and efficiency of oil extraction processes.