Casing pup joints, although often seen as simple extensions or fillers in oilfield tubular assemblies, are indeed crucial components in the oil and gas industry. These specialized short lengths of casing are utilized for various purposes, including spacing out full-length casings and accommodating necessary hardware in the wellbore. Their importance is highlighted by the need for precise engineering and manufacturing to ensure the structural integrity and performance of the overall system.
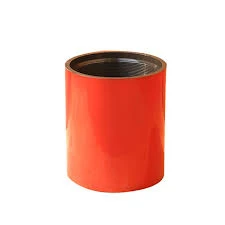
The engineering behind casing pup joints involves the use of high-grade steel that matches the specifications of the full-length joint they accompany. This is critical for maintaining consistent load-bearing capacities and ensuring seamless integration within the casing string. The material selection for these pup joints goes beyond mere conformity; it considers environmental factors such as temperature, pressure, and corrosive conditions specific to the well site. Therefore, expertise in metallurgy and a deep understanding of subterranean environments are crucial in creating casing pup joints.
Accuracy in the dimension specifications is another vital aspect of casing pup joints. These joints must be manufactured to exacting standards to function properly. Any disparity in diameter, thickness, or thread compatibility can compromise the integrity of the entire casing operation. This calls for a high level of precision in machining and threading processes, typically achieved using advanced computer numerical control (CNC) machines. Such precision ensures that the pup joints not only fit perfectly but also provide a leak-proof seal, essential in maintaining well control.
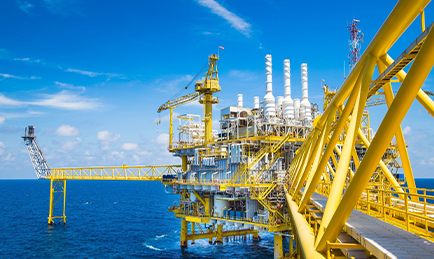
The installation and maintenance of casing pup joints require professional expertise. Drilling engineers and well operators must have a thorough understanding of the well architecture to determine the necessity and optimal placement of pup joints. During installation, these professionals rely on detailed engineering schematics and perform careful inspections to verify the integrity of the joints and connections. This expertise helps prevent common issues such as cross-threading or joint failure that can lead to costly operational downtimes.
In terms of authoritativeness, the companies manufacturing casing pup joints are usually accredited by international standards organizations. Certifications from bodies like the American Petroleum Institute (API) assure that these products meet global standards in quality and performance. Such certifications are a testament to the manufacturer's commitment to excellence and assure customers of the product's reliability in the field.
casing pup joint
Trustworthiness in the performance of casing pup joints is built over several factors. First, manufacturers often provide extensive records of stress tests, quality control checks, and field-performance reports. These documents demonstrate the capacity of casing pup joints to withstand operational stresses and highlight any operational limitations. Furthermore, after-sales support, including the availability of technical assistance and warranty terms, enhances trust between manufacturers and operators by ensuring that any issues are promptly addressed.
Beyond their technical specifications, casing pup joints play a strategic role in optimizing the cost-efficiency of oilfield operations. By facilitating precise depth control and allowing for fine adjustments to the drilling string without the laborious or costly need to cut custom casing lengths, they enable operators to maintain flexibility and responsiveness to dynamic drilling conditions. This adaptability can result in significant cost savings and increase the efficiency of rig operations.
Operators seeking the best casing pup joints often look for suppliers with a proven track record of success in various geographical and operational conditions. Such experience indicates a practical understanding of diverse well environments and enhances the supplier's ability to recommend the right solutions for specific project needs.
Overall, casing pup joints, though small components in the big picture of oilfield operations, embody a convergence of engineering precision, material science, and strategic utility. Their role is vital and multi-faceted, serving not just as extensions of casing strings, but as critical enablers of operational efficiency and safety. For operators and engineers, understanding the nuances of casing pup joints – from their material properties to the intricacies of their application – is essential for successful well management.