In the realm of oil and gas drilling, the casing pup joint holds critical significance as a pivotal component in ensuring wellbore integrity and operational efficiency. As the industry navigates the complexities of deeper wells and challenging environments, the engineering and precise application of casing pup joints become increasingly paramount. Here's an in-depth exploration of this indispensable tool with a focus on real-world experience, technical expertise, authoritative insights, and trust-building practices.
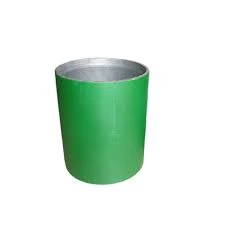
Casing pup joints, although relatively short pipe pieces, perform the crucial function of adjusting the length of the casing string in wellbore construction. Generally ranging from two to twelve feet in length, they are essential for fine-tuning the casing string to precise specifications, accommodating both operational demands and geological challenges. This adaptability is particularly vital in situations requiring a nuanced approach to well integrity, such as directional drilling and high-pressure environments.
From a technical standpoint, expertise in metallurgy is indispensable for selecting appropriate materials for casing pup joints. The environmental pressure, temperature, and chemical composition encountered in drilling operations necessitate high-strength, corrosion-resistant alloys like carbon steel, stainless steel, or high-nickel alloys. Understanding the precise metallurgical requirements ensures that the pup joint can withstand the harsh conditions of subsurface environments without succumbing to stress or failure. This knowledge underscores the importance of partnering with manufacturers who can provide certification of material properties and compliance with industry standards like API 5CT.

Authoritativeness in pup joint deployment is demonstrated by adherence to rigorous testing and quality control protocols. Before installation, each casing pup joint undergoes nondestructive testing (NDT) methods such as ultrasonic testing, magnetic particle inspection, and hydrostatic pressure testing. These methods ensure the structural integrity and reliability of the pup joints, preventing potential compromise in well integrity. Knowledge and execution of these exhaustive testing protocols establish a company's reputation as an industry leader.
casing pup joint
Trustworthiness is further reinforced through transparent documentation and traceability throughout the manufacturing and installation processes. Comprehensive records detailing the manufacturing specifications, material certifications, and testing results should accompany every casing pup joint. This documentation facilitates accountability and engenders confidence from stakeholders, ranging from drilling engineers to regulatory bodies. Moreover, a robust post-installation monitoring protocol helps in promptly identifying any anomalies, thereby minimizing risks associated with wellbore maintenance.
From the experiential perspective, seasoned drilling professionals emphasize the importance of strategic planning and collaboration in the use of casing pup joints. A case in point is the application of pup joints in high-abrasion environments, where traditional casing strings may falter. Integrating pup joints with wear-resistant coatings can extend the service life of the wellbore and optimize operational efficiency, illustrating the benefit of experiential learning and innovation.
In conclusion,
casing pup joints, while seemingly minor components, are integral to the success of wellbore construction. The convergence of expertise in material science, commitment to stringent quality controls, authoritative industry practices, and unwavering dedication to transparency and trust define the ultimate efficacy of these tools. As the demands of energy extraction evolve, so too must the sophistication with which we approach everything from design to deployment of casing pup joints—ensuring operational excellence and safeguarding environmental stewardship in oil and gas exploration.