Casing threads and couplings play a vital role in the integrity and efficiency of oil and gas drilling operations. Understanding these components' nuances can significantly impact a project's success, especially when considering the depth and complexity of modern extraction sites.
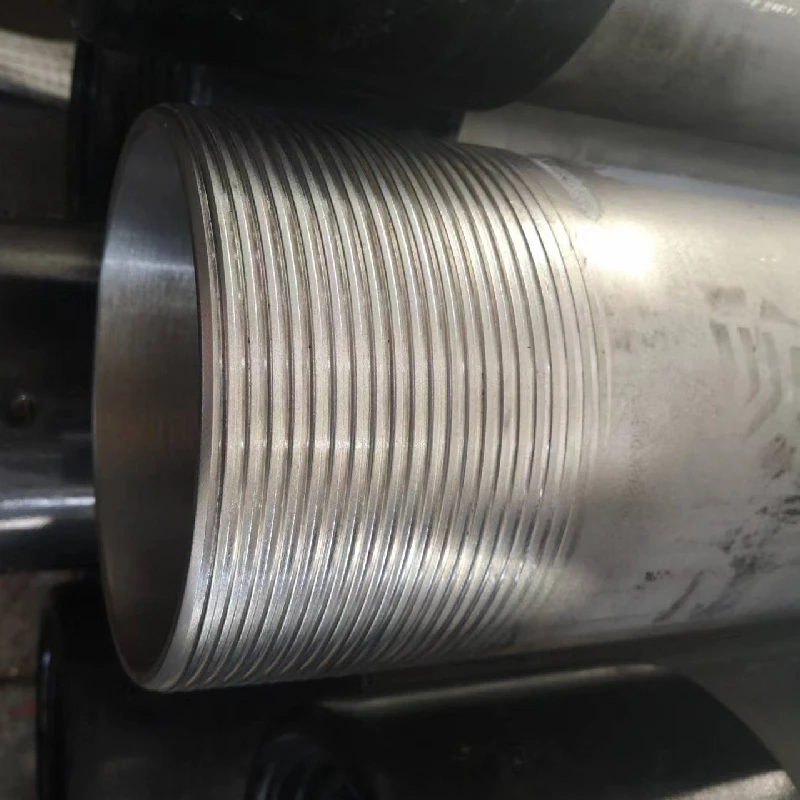
The world of casing threads is diverse, with many options available depending on the specific geological conditions and objectives of the drilling project. Casing threads refer to the spirals cut into the ends of pipes to ensure a tight connection between pieces. The threading complements the coupling, which is a special connector that joins lengths of pipes. A precise fit between the two ensures not only structural integrity but also prevents the dangerous escape of hydrocarbons.
Precision in the threading process cannot be overstated. Misaligned or poorly cut threads can lead to catastrophic failures, including pipe leaks and breakages under pressure. API connections, for instance, are widely recognized for their robust standards in oil and gas operations. Their universal threading standards offer ease of use and interchangeability, reducing downtime caused by mismatches. However, for more challenging environments, premium threads provide added durability and performance due to their advanced sealing capabilities and high-pressure resistance.

From the perspective of expertise, coupling selection is as critical as thread selection. While the primary function of couplings is to connect pipes securely, the material and design can affect overall performance. Standard couplings are usually made from carbon steel, which offers a good balance of strength and cost-effectiveness. For more corrosive environments, alternative materials such as stainless steel or alloys like Inconel are preferred due to their exceptional resistance to harsh chemicals and extreme temperatures.
Trust in manufacturers' certifications is essential when selecting casing threads and couplings. Look for products that adhere to stringent API standards or, in the case of specialty threads, those that come with proprietary certifications and detailed specs. Relying on established brands with proven track records is prudent. Not only does this ensure product reliability and consistency, but it also enhances the credibility of the entire drilling operation.
casing threads and couplings
Hands-on experience adds a layer of insight that purely theoretical knowledge cannot replicate. Industry veterans know that even the best threads and couplings can fail under challenging conditions if not properly handled. The right torque, alignment, and maintenance practices can prevent many issues. Implementing regular inspections and precise installation protocols are strategies that have proven effective in mitigating risks and extending the lifespan of these critical components.
The authority of expert reviews and field studies should also influence product selection and deployment strategies. Peer-reviewed case studies or documented field trials can offer invaluable data, showcasing performance in real-world situations. These pieces of evidence provide a benchmark for evaluating prospective options and gauging how they might react under similar pressures and stresses.
To align these insights with the principles of effective SEO, weaving this deep knowledge into web content can attract experts in the field searching for advanced information. Consistently updated content reflecting the latest industry standards, trends, and real-world applications can significantly boost search rankings and authoritativeness. Ensuring the webpage is technically optimized, with fast loading times and mobile responsiveness, further enhances the trustworthiness metric which search engines value highly.
In sum, the precision and compatibility of casing threads and couplings not only define operational efficiency but can also prevent potentially hazardous situations. The key lies in selecting high-quality materials, applying deep industry knowledge, and adhering to best practices to ensure these components can withstand the rigors of modern drilling operations. Only through consistent performance and reliability can these integral parts uphold the safety and success of oil and gas ventures.